Lösungen für Verzug im 3D-Druck
Simulation für Funktions-Bauteile
Durch Temperaturunterschiede während des Aufschmelzprozesses und Zwängungen entstehen Spannungen in 3D-Druck-Bauteilen, die zu Verzug führen können. Ein Problem, wenn es um maßhaltige und sicherheitsrelevante Bauteile geht. Durch Simulationstechniken lassen sich nach Merkle & Partner diese Herausforderungen bereits zufriedenstellend lösen.
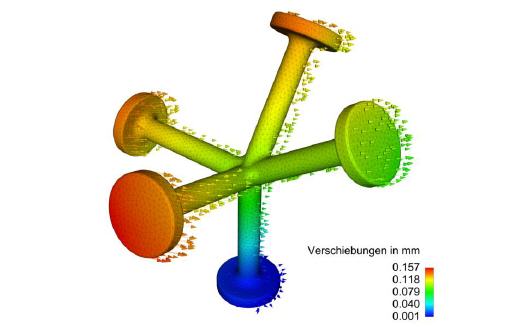
Im 3D-Druck wird schichtweise Metallpulver verschmolzen. Während des Laserprozesses im SLM-Verfahren werden Schichten des flüssigen Metalls mit bis zu 1.250°C auf bereits stark abgekühlte Schichten geschmolzen. Diese Konstellation kann zu Spannungen und Zwängen innerhalb des Bauteils führen und folglich zu Delamination, Rissen oder Verzug – für sicherheits- sowie funktionsrelevante Bauteile ernstzunehmende Faktoren.
Gemeinsam mit der Hochschule Aalen forscht das Ingenieurbüro Merkle & Partner im Rahmen des Projektes ROAD3D (Robuste Auslegung und Dimensionierung sicherheitsrelevanter Bauteile für den 3D-Metalldruck) unter anderem an Lösungen, um diese Effekte simulativ abzubilden.
„Ein wichtiger Aspekt ist die Abstimmung der Simulation am entsprechenden 3D-Drucker. Diese Form der Kalibrierung erfolgt anhand des Drucks einer definierten Teststruktur. Der gedruckte Testkörper wird vermessen, Abweichungen werden analysiert und die jeweiligen Parameter in der Simulation angepasst. Damit erhält man eine für den spezifischen Drucker adaptierte Simulation. Diese Methode ist technische wie wirtschaftlich notwendig, da aktuell nicht alle Effekte der additiven Fertigung mit vertretbarem Aufwand simulativ abgebildet werden können. Allerdings muss diese Kalibrierung nur einmal durchgeführt werden“, so Dr.-Ing. Maik Brehm, Verantwortlicher für das Projekt ROAD3D bei Merkle & Partner.
Sind die Parameter der Simulation einmal kalibriert, können sehr genaue Vorhersagen hinsichtlich der Temperaturentwicklung und dem damit verbundenen Verzug oder der Rissbildung getroffen werden. Eine Optimierung der Prozessparameter oder eine Anpassung der Geometrie und Stützstrukturen kann dann zielgerichtet virtuell durchgeführt werden. Im Vergleich zum iterativen Verfahren, über mehrere reale 3D-Drucke, ist die Vorgehensweise über die Simulation eine weitaus exaktere und zeitsparendere Methodik.
Darüber hinaus sind bereits viele Effekte in der Simulation im zehntel-Millimeter-Bereich abbildbar. So lassen sich Abweichungen vorhersagen und der Verzug kann bereits in der Konstruktion des Bauteils kompensiert werden.
Der 3D-Druck bietet noch ungenutzte Möglichkeiten für Bauteile mit integrierten Funktionen, wie beispielsweise Kühl-Düsen im Maschinenbau. Über 3D-Druck können komplexe Strömungskanäle innerhalb des Bauteils integriert werden. Dies führt zu einer höheren Effektivität, gezielteren Funktion und gesteigerten Energieeffizienz. Genau für derartige Entwicklungen birgt der 3D-Druck enormes Potenzial.
„Die virtuelle Entwicklung eines 3D-gedruckten Bauteils mittels Simulation ist der Türöffner für die Entwicklung von Bauteilen, die wir uns heute oftmals noch gar nicht vorstellen können. Ideen für funktionsintegrierte Bauteile scheinen bereits zuhauf in Schreibtisch-Schubladen zu schlummern. Der zeitliche wie finanzielle Aufwand stoppt aktuell noch Innovationen. Dies könnte die verstärkte Nutzung von Simulationstechnologien in der Design- und Fertigungsphase ändern“, ergänzt Brehm.
Mehr Informationen zu Merkle & Partner:
![]() |
MERKLE & PARTNER GbR |
![]() |
Ingenieurbüro für Simulation & Entwicklung |
![]() |
Friedrichstraße 1 |
![]() |
89518 Heidenheim |
![]() |
Tel.: +49 (0)7321 9343-0 |
![]() |
Fax: +49 (0)7321 9343-20 |
![]() |
E-Mail: info@merkle-partner.de |
![]() |
www.merkle-partner.de |
War dieser Artikel für Sie hilfreich?
![]() |
![]() |
![]() |
![]() |
![]() |
Bitte bewerten Sie diese Seite durch Klick auf die Symbole.
Zugriffe heute: 3 - gesamt: 4307.