Wenn sich die Durchlaufzeit halbiert...
Take-off auf Augenhöhe
Krüger Aviation setzt bei der Kunststoffnachbearbeitung
auf eine 5-Achs-CNC-Gantry-Fräsanlage von HG Grimme SysTech.
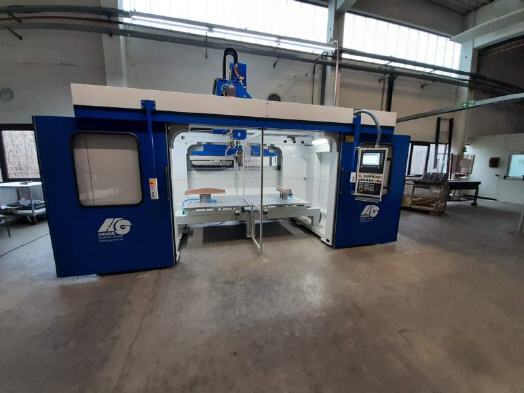
Die Luftfahrtindustrie zählt zu den anspruchsvollsten Kunden von Bauteilherstellern: Daher arbeiten für sie nur zuverlässige, zertifizierte Zulieferer, die bei der Wahl ihrer Produktionsmittel verständlicherweise sehr wählerisch sind. Doch was macht ein Traditionsunternehmen wie Krüger Aviation, das kurzfristig eine extrem anspruchsvolle Maschine zur Kunststoffnachbearbeitung braucht?
Die Referenzliste der Krüger Aviation GmbH aus Barsbüttel bei Hamburg liest sich wie das Who-is-who der Luftfahrtindustrie: Das hanseatische Traditionsunternehmen beliefert mehr als 300 Firmen der Branche – von Airbus, Lufthansa Technik, Safran bis hin zu ZIM Flugsitz. Gefragt sind die Bauteile außerdem bei Herstellern von Schiffen und Eisenbahnen. 40 Mitarbeiter stellen per Thermotiefziehen, CNC-Zerspanen und 3D-Druck Halbzeuge sowie komplexe Fertigteile und Baugruppen aus Kunststoff her.
„Wir helfen unseren Kunden, Bauteile auszulegen, zu zertifizieren oder auch beim Wechsel von einem Fertigungsverfahren auf ein anderes“, erklärt Florian Ehinger, Head of Customer Service. „Zunehmend kommen aber auch Kunden mit einem Aluminium-Bauteil und fragen: Könnten Sie uns einen Kunststoff vorschlagen, den wir da vielleicht statt Alu einsetzen könnten?“
Optische Qualität spielt wichtige Rolle
Zu den besonderen Spezialitäten zählen hochwertige Spiegel aus Spezialkunststoff, bei denen die Norddeutschen zu den weltweit führenden Anbietern gehören und für die sie mehrfach Preise wie den „Crystal Cabin Award“ erhielten. Außerdem entstehen in Barsbüttel per Kunststofftiefziehen u.a. aus Polycarbonat (PC), Polyamid (PA 66) oder Polyphenylsulfon (PPSU) Leuchten- und Sitzarmaturen-Abdeckungen sowie andere Bauteile für den Kabinen- und Toilettenbereich. Doch alle Bauteile besitzen einen gemeinsamen Nenner: Es sind sogenannte Sichtteile ohne tragende Funktion. Ehinger: „Bei allen unseren Bauteilen spielt die optische Qualität eine wichtige Rolle. Wir betreiben hier deshalb einen sehr hohen Aufwand.“
Just-in-Time-Lieferung lautet eine weitere Anforderung: Die Luftfahrtindustrie besteht auch bei den meist in kleinen Losgrößen und maßgeschneidert hergestellten Komponenten auf extrem kurze Lieferzeiten. Daher optimiert Krüger Aviation alle Prozesse von der Entwicklung, der Produktion bis hin zum Handling. Doch wie geht ein in der vierten Generation geführtes Traditionsunternehmen mit über 100jähriger Firmengeschichte vor, wenn es kurzfristig eine zugleich hoch präzise und extrem schnelle Fräsmaschine für die Nachbearbeitung von Kunststofftiefziehteilen, das sogenannte Beschnittfräsen, braucht?
Maschinensuche führt ins Unterallgäu
Die Norddeutschen nahmen zunächst die Maschinen von bekannten Unternehmen aus der Nähe unter die Lupe, stießen dann aber auf die HG Grimme SysTech GmbH aus Wiedergeltingen im Landkreis Unterallgäu. Für HG Grimme spricht, dass es sich ebenso wie Krüger Aviation um ein familiengeführtes, mittelständisches Unternehmen handelt. Außerdem hat es sich auch auf eine High-Tech-Nische der Kunststoffverarbeitung spezialisiert. Bereits seit den 1980er Jahren entstehen dort CNC-Bearbeitungszentren zur Nachbearbeitung von Tiefziehteilen, damals eine Rarität in Deutschland. Seit 2010 bauen die Bayern auch CNC-Gantry-Bearbeitungszentren.
Doch nicht nur die Kompetenz in Sachen Kunststoffverarbeitung und die Betreuung auf Augenhöhe überzeugen die Norddeutschen. „HG Grimmes Leistungspotenzial für unsere Form der Kunststoffnachbearbeitung ist für uns ideal“, sagt Ingo Horster, Chief Technical Officer (CTO) bei Krüger Aviation. „Und dann stand dort auch noch eine 5-Achs-CNC-Gantry-Fräsanlage, die von der kompakten Größe und ihrer Leistung her genau passte. HG Grimme nahm an der Vorführmaschine nur noch geringfügige Anpassungen vor. Und schon konnten wir nach kurzer Zeit das Beschnittfräsen von Tiefziehteilen starten.“
Der Begriff „geringfügige Anpassungen“ ist wahrscheinlich hanseatischem Understatement geschuldet, denn Krüger Aviation hatte einen besonderen Wunsch: Als Werkstückaufnahme haben die Norddeutschen einen Vakuum-Spanntisch entwickelt, der zusammen mit Halbzeugen sogar komplexe geformte Bauteile bei hohen Frästempo prozesssicher und schwingungsfrei aufnimmt. Bisher wurde der selbst entwickelte Vakuum-Spanntisch aus Holz oder Uriol gefertigt. HG Grimme sollte nun eine solide Vollaluminium-Variante herstellen. Der Wunsch zum noch robusteren Spanntisch ist nachvollziehbar, zerspant doch die neue Gantry in der X/Y-Achse mit einer Geschwindigkeit von bis zu 80 Metern pro Minute.
„Wir können jetzt auf einer Maschine Bauteile in mit drei und fünf Achsen bearbeiten“, freut sich der CTO. „Jetzt gelingt es uns sogar, synchron links und rechts verschiedenste Artikel gleichzeitig zu fräsen.“ Eine abnehmbare Trennwand aus Makrolon ermöglicht es, auf der einen Tischseite zu rüsten, während auf der anderen gefräst wird. Bewährt hat sich hier auch, dass der Balken mit dem Fräskopf nicht von vorne nach hinten, sondern von links nach rechts fährt. Der Bediener kann daher während des Fräsprozesses auf der zweiten Tischseite völlig ungestört arbeiten. Horster lobt das nun dynamischere und zugleich stabilere Zerspanen. Außerdem arbeitet die CNC-Anlage in Gantry-Bauweise trotz des hohen Frästempos so präzise im µm-Bereich, sodass nachträgliches Polieren oft entfällt.
Dynamisch Zerspanen mit einseitig gelagertem Fräskopf
Ein ungewöhnlicher Anblick für Experten für Metallbearbeitung ist der sehr kompakte Fräskopf, der sich maximal 540° Grad drehen und bis 365° schwenken kann. „Weil hier nicht wie in der Metallverarbeitung hohe Kräfte auftreten, können wir mit einem einseitig gelagerten Fräskopf arbeiten“, erläutert Horster. „Mit ihm fräsen wir auch die typisch filigranen Werkstücke sehr dynamisch, denn wir können den Kopf nun sehr weit nach unten schwenken, ohne dass dabei die Gefahr entsteht, dass der Fräskopf mit Tisch oder den Aufnahmen kollidiert.“ Das Kollisionsrisiko falle nun viel geringer aus als bei der vorherigen Maschine.
Gut fielen die Erfahrungen mit den ersten gefrästen Bauteilen aus. Krüger Aviation startete zunächst mit Thermoform-Halbzeuge aus dem Kunststoff Uriol und testet nun auch Bauteile aus anderen Kunststoffen für die Luftfahrtindustrie, bei denen dann die „first article inspection“ durch die Kunden ansteht. „Bis jetzt funktioniert alles hervorragend“, berichtet Horster. „Wir stehen beim Fräsen zwar nicht mit der Stoppuhr da: Aber definitiv ist es so, dass sich die Durchlaufzeit pro Werkstück um die Hälfte reduziert hat.“
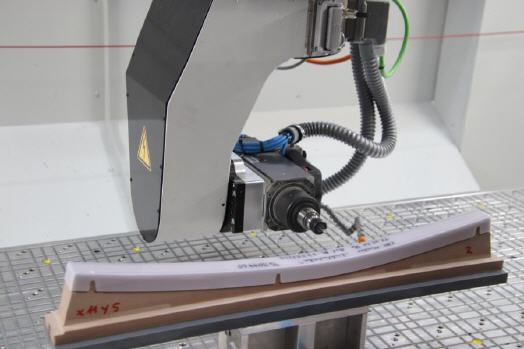
Mehr Informationen zu HG Grimme Systech:
![]() |
HG GRIMME SysTech GmbH |
![]() |
Osterweg 23 |
![]() |
86879 Wiedergeltingen |
![]() |
Tel.: +49 82 41 96 08 0 |
![]() |
Fax: +49 82 41 96 08 55 |
![]() |
E-Mail: info@hg-grimme.de |
![]() |
www.hg-grimme.de |
War dieser Artikel für Sie hilfreich?
![]() |
![]() |
![]() |
![]() |
![]() |
Bitte bewerten Sie diese Seite durch Klick auf die Symbole.
Zugriffe heute: 5 - gesamt: 4459.