Ideales Konzept
MSF Compact von Microstep als Problemlöser
Die HSB Group produziert Schwimm- und Erlebnisbecken aus Edelstahl für den kommunalen Bedarf. Dabei sind präzise Einzelteile für maßgenaue, große Edelstahl-Dünnblechkonstruktionen gefragt. Ein MSF Compact löste die bestehenden Produktivitätsdefizite und schuf enorme Flexibilität.
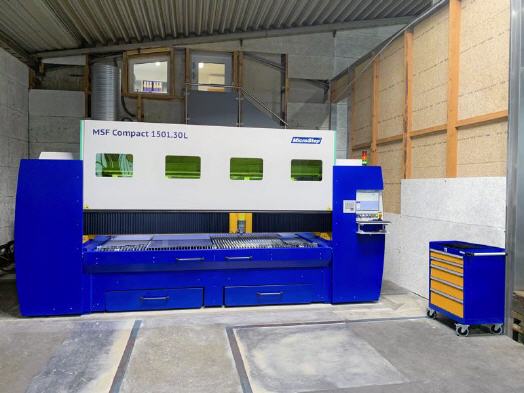
Wasser ist Leben. Aber auch Erholung, Spaß, Therapie. Egal welches Alter – Generationen erfreuen sich beim Schwimmen, Rutschen oder Planschen. Damit die Freude lange anhält und auch unabhängig von Baggerseen und Jahreszeiten funktioniert, ist entsprechende Infrastruktur notwendig. Einen elementaren Baustein liefert seit 1969 die HSB Gruppe. Denn vor mehr als 50 Jahren installierte der Pionier der Schwimmbadherstellung in Österreich das erste Schwimmbecken aus Edelstahl. Es war zudem das erste weltweit – und das ist auch heute noch in Betrieb. Dank des Materials Edelstahl sowie viel Präzision und Know-how bei der Verarbeitung, Konstruktion und Projektierung von Schwimm- oder Erlebnisbecken sind die Produkte für viele Generationen nutzbar.
In ganz Europa sind die Erzeugnisse der Gruppe mit unterschiedlichen Standorten und rund 140 Mitarbeitern gefragt. Mehr als 2000 Anlagen wurden seit Beginn ausgeliefert, das entspricht rund 6000 Becken. „Pro Anlage verarbeiten wir 20 bis 70 Tonnen Edelstahl. Dabei handelt es sich um ein äußerst nachhaltiges Produkt. Denn aus einer Tonne Edelstahl kann ich 20 Quadratmeter Becken bauen, aus einer Tonne Beton lediglich 2“, erklärt Dr. Alois Dachs, Geschäftsführer der HSB Austria GmbH. Die Gesellschaft kümmert sich um Kunden in Deutschland, Österreich, der Schweiz, Frankreich und Skandinavien.
Rund 800 Tonnen Edelstahl verarbeitet der Betrieb jährlich in den Produktionen in Vöcklamarkt in Oberösterreich und Berlin Spandau. Rund zehn Hersteller sind europaweit in diesem Segment vertreten. „Wir haben den Anspruch Qualitäts- und Marktführer zu sein“, sagt Dr. Dachs. Die Herausforderung dabei: „Die Edelstahlwand ist eine Dünnblechkonstruktion mit 2 bis 2,5 mm Dicke, die durch Verschweißen entsteht. Die Teile sind bis zu fünf Meter lang und 2,20 m hoch. Das muss sehr genau und verzugsfrei hergestellt werden.“ Beim Schwimmsport beispielsweise gäbe es Toleranzen von unter 1 cm auf 50 m Länge einzuhalten.
Viele Jahre baute das Unternehmen beim Zuschnitt der maßgenauen Bleche auf externe Lieferanten oder Bearbeitung durch eine Stanz-Nibbelmaschine. Dabei müssen in die 1,5 bis zu 10 mm starken Bleche viele Lochbilder und auch unterschiedlichste komplexe Konfigurationen geschnitten werden. Bei zugekauften Teilen mangelte es an Geschwindigkeit und an Flexibilität, bei der Stanz-Nibbelmaschine war jedes Mal aufwendiges Entgraten notwendig. „Das war immer ein Hemmschuh. Wir sind im Baunebengewerbe und da verschieben sich einzelne Projekte von der einen auf die andere Woche. Dann muss die Produktionsreihenfolge von einem Tag auf den anderen umgestellt werden können.“
Umstände, die dank einer Neuinvestition der Vergangenheit angehören. Denn seit Mitte 2020 setzt das Unternehmen auf eine eigene Schneidlösung: ein 2D-Faserlasersystem der Baureihe MSF Compact von MicroStep mit einer Bearbeitungsfläche von 1.500 x 3.000 mm. „Wir sind vollauf zufrieden. Unsere Leute sind alle begeistert. Unser Produkt besteht aus sehr viel Handarbeit. Da ist jeder sehr froh, dass wir Teile auf diese Weise flexibel handhaben können“, zieht der Geschäftsführer ein Zwischenfazit.
Das platzsparende Lasersystem wird rund ein Drittel im Einschichtbetrieb ausgelastet. Für HSB Austria dennoch eine lohnende Investition nach fokussierter Suche. „Da wir beengte Platzverhältnisse haben, war uns eine kompakte Bauweise sehr wichtig. Zuerst haben wir bei den üblichen Verdächtigen in der Branche angefragt, uns im Internet und unserem Umfeld umgeschaut. Über eine Internetrecherche sind wir dann auf MicroStep gestoßen. Das Konzept der Anlage ist für uns ideal und auch das Preis-Leistungsverhältnis ist sehr gut.“
Der Plan der Anschaffung ging vollends auf. „Wir haben damit Flexibilität eingekauft. Wichtig ist, dass wir möglichst viele Elemente möglichst präzise herstellen können. Das deckt der Laser ab. Wir haben die Nacharbeiten stark reduziert und damit steigt auch für unser Personal die Arbeitsplatzqualität.“
Mehr Informationen zu Microstep:
![]() |
MicroStep Europa GmbH |
![]() |
Messerschmittstraße 10 |
![]() |
86825 Bad Wörishofen |
![]() |
Tel.: +49 8247 96294-00 |
![]() |
Fax: +49 8247 96294-09 |
![]() |
E-Mail: info@microstep.com |
![]() |
www.microstep.com |
War dieser Artikel für Sie hilfreich?
![]() |
![]() |
![]() |
![]() |
![]() |
Bitte bewerten Sie diese Seite durch Klick auf die Symbole.
Zugriffe heute: 3 - gesamt: 4370.