Der Laser als flotter Glasschneider
Ein besserer Weg zum Weinglas
Weingläser werden seit Jahrtausenden verwendet und kaum jemand würde sie als „Hightech“ bezeichnen. Die iProtec GmbH, ein Unternehmen, das Produktionsanlagen zur Herstellung von Trinkgläsern entwickelt und fertigt, hat jedoch eines der modernsten verfügbaren Laserverfahren zur Entfernung der prozessbedingten Glaskappe bei Gläsern entwickelt und bietet dieses heute in automatisierten Systemen an. Hierbei wird das Glas mittels eines Ultrakurzpulslasers und des SmartCleave-Prozesses von Coherent geschnitten, was zu hervorragenden Ergebnissen, reduzierten Kosten und einer umweltfreundlicheren Fertigung führt.
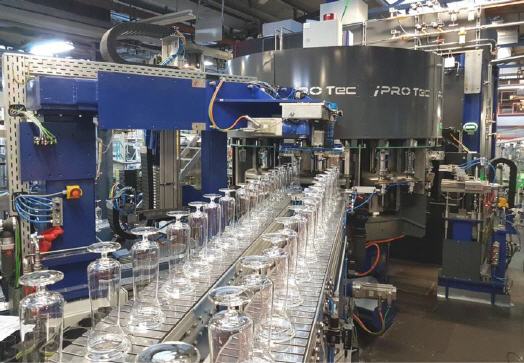
iProtec (Zwiesel/Niederbayern) wurde 2006 gegründet und 2011 von den Eigentümern der Zwiesel Kristallglas AG übernommen. Alle drei Schwesterunternehmen – Zwiesel Kristallglas AG, Ullrich GmbH und iProtec GmbH – befinden sich alle am gleichen Standort. iProtec beschäftigt mittlerweile über 160 Mitarbeiter. Der Unternehmensschwerpunkt liegt auf automatisierten Anlagen zur Herstellung von Trinkgläsern. Dabei ist iProtec das einzige Unternehmen, dessen Maschinen alle Schritte des Produktionsprozesses von Hohlgläsern abdecken.
Darüber hinaus beliefert iProtec die Automobilindustrie unter anderem mit Montage-, Klebe-, Prüf- und Schweißsystemen und fertigt eine Vielzahl spezialisierter Produktionsanlagen nach spezifischen Kundenanforderungen. Eigene Design-, Beschaffungs-, Elektro-, Fertigungs- und Montageabteilungen sorgen für hohe Flexibilität und perfekten Kundenservice.
iProtec verfolgt einen ganzheitlichen Ansatz bei der Anlagenentwicklung. Das Ziel sind Systeme, die sich nahtlos in die bestehende Produktionslandschaft der Kunden integrieren. Ein Schwerpunkt der Bemühungen liegt auf der Senkung der Produktionskosten bei gleichzeitiger Verbesserung von Qualität und Ertrag. Die Implementierung umweltschonender Herstellungsverfahren sind dem Unternehmen dabei besonders wichtig.
Bei der Weinglasherstellung wird ein Tropfen geschmolzenen Glases in eine Form gebracht. Anschließend wird Luft in den Tropfen geblasen, damit er sich ausdehnen und die Form ausfüllen kann.
Das Glas kühlt in der hohlen Form ab, wobei produktionsbedingt eine „Glaskappe“ (das Überglas) entsteht. Diese Kappe wird in den späteren Produktionsschritten zum Halten und Handhaben des Glases benötigt – beispielsweise um Glasstiel oder -boden zu befestigen – und erst danach entfernt. Die Kante, die durch das Entfernen der Kappe entsteht, bildet letztlich den Trinkrand des fertigen Glases, an dem die Lippen ansetzen, und darf deshalb keine scharfen Ränder aufweisen.
Die konventionell eingesetzten Technologien zum Entfernen des Überglases lassen sich in zwei Hauptgruppen einteilen – nämlich das Entfernen des Deckels bei heißen oder bei kalten Gläsern. Die Kappe kann also durch Erwärmen des Glases oder durch Anritzen des Mundrandes und Verwendung von Thermoschock abgetrennt werden. Bei letzterer Methode wird die Kappe anschließend mechanisch entfernt. Dies kann durch einen Luftstoß oder einen mechanischen Impuls erfolgen.
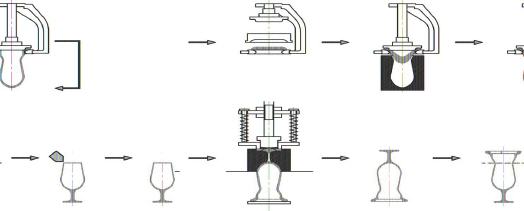
Laser ersetzt Flamme
In jüngerer Zeit hat der CO2-Laser die bisher verwendete Flamme zum Erwärmen des Glases abgelöst. Ein weiterer Schritt zum physischen Entfernen der Kappe ist bei dieser Methode aber ebenfalls erforderlich. Oftmals erzeugen Trennverfahren eine geringere Qualität als für das fertige Glas gefordert. Häufig müssen verschiedene Nachbearbeitungsschritte wie mechanisches Schleifen und Facettieren eingesetzt werden, um die gewünschte Oberflächenqualität zu erreichen, was zusätzlichen Zeit- und Kostenaufwand bedeutet.
Das Schleifen benötigt zudem Wasser und erzeugt Glasreste – beides mit Auswirkungen auf die Umwelt. Darüber hinaus müssen die Gläser im Anschluss unter Einsatz von Energieverbrauch getrocknet werden. Die mechanischen Kräfte beim Schleifen wiederum können zu Bruch führen. Da die Wanddicke von Glas zu Glas variieren kann, sind beide Schneidprozesse zudem nicht vollständig reproduzierbar.›Filamentierung‹ ist ein alternatives Glastrennverfahren zu thermischen beziehungsweise mechanischen Verfahren mittels Flamme oder CO2-Laser. Genutzt werden dabei sehr hohe Leistungsdichten, die mit einem Ultrakurzpulslaser selbst bei geringer Gesamtlaserleistung erreicht werden können.
Die patentierte Version dieses energieeffizienten Prozesses von Coherent heißt ›Smartcleave‹. Das Verfahren ermöglicht das Hochgeschwindigkeitsschneiden von geraden Linien, Kurven und Einsätzen ohne Schnittspalt in transparente und spröde Materialien mit einer Dicke von 50 µm bis 10 mm. Smartcleave ermöglicht ebenfalls glatte Oberflächen mit einer Rauheit (Ra) von weniger als 1 µm und Ausmuschelungen von weniger als 5 µm. Und vor allem führt es zu einer Biegefestigkeit, die den mechanischen Verfahren messbar überlegen ist, was es beispielsweise für Touchscreen-Hersteller besonders attraktiv macht.
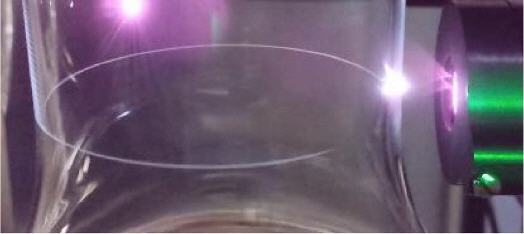
Nachteile aufgehoben
Beim Entfernen der Weinglaskappen hebt Smartcleave praktisch alle Nachteile des Brenn- oder CO2-Laserschneidens auf. Die Laserenergie wird räumlich so präzise und begrenzt eingesetzt, dass es zu keiner Erwärmung des Glases und damit zu keiner thermischen Schädigung des Materials kommt. Es entsteht eine extrem glatte Kante ohne Grate, Risse oder Ausbrüche, wodurch sich jegliche Nachbearbeitung erübrigt. Somit entfallen alle zusätzlichen Schleif-, Wasch- und Trocknungsschritte sowie deren Energieverbrauch, Zeitaufwand, Kosten und Umweltauswirkungen (kein Staub und Niederschlag auf den Gläsern). Smartcleave erhöht den Ertrag, verbessert die Qualität und senkt die Produktionskosten.
Für das Filamentschneiden mittels Smartcleave wird der Laserstrahl eines Ultrakurzpulslasers (< 15 Pikosekunden) auf einen kleinen Punkt im Glassubstrat fokussiert. Die sehr hohe Laserstrahlintensität bewirkt eine Selbstfokussierung des Strahls (durch den optischen Kerr-Effekt) im Glas. Diese Selbstfokussierung erhöht die Leistungsdichte weiter, bis ab einem bestimmten Schwellenwert ein Plasma mit niedriger Dichte im Material entsteht. Dieses Plasma senkt den Materialbrechungsindex in der Mitte des Strahlenganges und bewirkt, dass der Strahl defokussiert wird. Wenn die Strahlfokussieroptik richtig konfiguriert ist, kann dieser Fokussierungs-/Defokussierungseffekt ausgeglichen werden, um sich periodisch zu wiederholen und sich selbst zu erhalten. So entsteht ein stabiles Filament, das heißt, eine Reihe winziger Hohlräume, die sich über mehrere Millimeter tief in das Glas hinein erstrecken. Der typische Filamentdurchmesser liegt im Bereich von 0,5 µm bis 1 µm.
Beim Schneiden wird das Glas quer zum Strahl bewegt, um eine Reihe von engen, lasergenerierten Filamenten zu erzeugen. Je nach Materialstärke und gewünschter Schnittgeometrie kann eine Bewegungsgeschwindigkeit von 100 mm/s bis 2 m/s realisiert werden. Bei chemisch oder thermisch gehärtetem Glas führt die innere Spannung im Bauteil dann zu einer spontanen Separation, ohne zusätzlichen Bearbeitungsschritt.
Bei nicht gehärteten Gläsern und anderen transparenten Materialien wie etwa Saphir ist nach dem Smartcleave-Prozess ein zusätzlicher Schritt zum Separieren erforderlich. Dies kann entweder durch geringe mechanische Kraft oder durch thermische Spannung geschehen. Letzteres wird beispielsweise oft durch Erhitzen mit einem CO2- oder CO-Laser oder auch einer Flamme erreicht.
Ein Schlüsselfaktor für die praktische Umsetzung des Smartcleave-Schneidens ist der Einsatz eines UKP-Lasers, der den sogenannten ›Burst-Modus‹ ermöglicht, wie beispielsweise der Coherent ›HyperRapid NX‹. Im Burst-Modus liefert der Laser eine Reihe von Pulsen in engem zeitlichem Abstand. Ist der Zeitpunkt zwischen den nachfolgenden Pulsen im Burst kürzer als die Wärmediffusionszeit des Materials, baut sich im Glassubstrat Wärme auf, was die Glasverformbarkeit erhöht. Dadurch entsteht ein sanfteres und somit spannungsärmeres lokales Heizprofil als bei einer Reihe von Impulsen mit äquivalenter Energie, die über einen längeren Zeitraum abgegeben werden.
Dieser schonendere Wärmezyklus bringt mehrere wichtige Vorteile mit sich. Erstens erhöht er die Schnittgeschwindigkeit um bis zu Faktor zwei. Des Weiteren entstehen Löcher, die glatter und gerader sind als beim Einzelpuls-Filamentschneiden. Zudem eliminiert er die Bildung von Mikrorissen an den Lochrändern. Dies ist wichtig, da Mikrorisse die Glasfestigkeit deutlich verringern können.
iProtec hat ein vollautomatisches System entwickelt und zur Marktreife gebracht, welches das Smartcleave-Verfahren zur Entfernung des Überglases nutzt. Im Einsatz ist dort ein Coherent Powerline Smartcleave Sub-System, das auf einem Hyperrapid NX-Laser mit 50 W durchschnittlicher Ausgangsleistung und einer Wellenlänge von 1064 nm basiert. Das Sub-System umfasst mehrere optische Komponenten, Strahlweichen, Sensoren und Elektronik. Alles wird durch die Lasersteuerung von Coherent gemanagt, einschließlich eines Laserschutzkonzepts, das sich problemlos in das Sicherheitskonzept des iProtec-Systems integrieren lässt. Je nach Konfiguration und Einsatz der Anlage können bis zu 80 Gläser pro Minute verarbeitet werden.
Das iProtec-System ist die erste mit Smartcleave-Technologie ausgestattete Trinkglasschneidanlage auf dem Markt. Damit ermöglicht das Unternehmen seinen Kunden eine Senkung des Energieverbrauchs bei gleichzeitiger Ertragssteigerung und weniger Ausschuss. Das System hat sich im praktischen Einsatz bewährt und gewährleistet die von großen Trinkglasherstellern geforderte 24/7-Zuverlässigkeit.
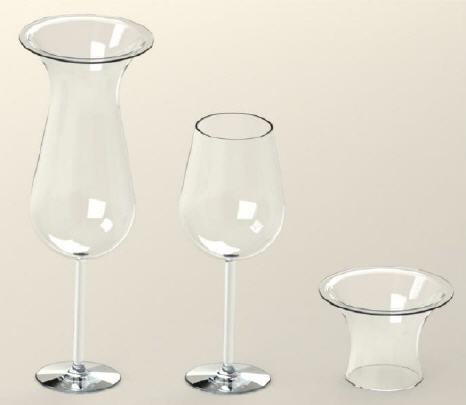
Ideale Technologie
»Wir haben schon frühzeitig bei der Entwicklung unserer aktuellen Systeme zur Glaskappenentfernung festgestellt, dass das Smartcleave-Schneiden einen enormen Nutzen für unsere Endanwender bietet«, sagt Tobias Bredl, Projektleiter bei iProtec.
»Wir haben Coherent als unseren Lieferanten für Laser-Sub-Systeme ausgewählt, da Coherent uns bei der Entwicklung des Prozesses und der Technologie unterstützen konnte und wollte. Dies ist uns besonders wichtig, wenn wir zum ersten Mal eine neue Technologie implementieren, die wir nicht kennen. Wir wollten keine Laserexperten werden müssen, um Smartcleave nutzen zu können. Dank der Bereitschaft von Coherent, das notwendige Wissen und die entsprechenden Produktlösungen zur Verfügung zu stellen, konnten wir die Markteinführungszeit verkürzen und unsere Gesamtentwicklungskosten senken. Außerdem gefiel uns der HyperRapid NX-Laser aus mehreren Gründen gut. Er setzt den Burst-Modus sehr effektiv um und bietet bewährte Zuverlässigkeit. Zudem macht sein kompaktes Design die Integration in unsere Maschinen sehr einfach. Dazu kommt, dass Coherent Laser, Sub-Systeme und Systeme durch ein starkes, globales Servicenetzwerk unterstützt werden. Das ist uns wichtig, denn wir versenden unsere Anlagen in die ganze Welt.«
Download
Diesen Artikel finden Sie auch in Heft 1/2021 auf Seite 58. Zum besagten Heft führt ein Klick auf den nachfolgenden Button!
Mehr Informationen zu Coherent:
![]() |
Coherent Shared Services B.V. |
![]() |
Dieselstr. 5b |
![]() |
64807 Dieburg |
![]() |
Tel.: 06071 – 968 – 0 |
![]() |
E-Mail: sales.germany@coherent.com |
![]() |
www.coherent.de |
War dieser Artikel für Sie hilfreich?
![]() |
![]() |
![]() |
![]() |
![]() |
Bitte bewerten Sie diese Seite durch Klick auf die Symbole.
Zugriffe heute: 2 - gesamt: 4657.