Kunstharz-Anlagen für die Rotorblatt-Produktion
Mehr Automation und Qualität im Prozess
Rund um den Globus leisten die Dosier-, Misch- und Entgasungsanlagen von TARTLER ihren Beitrag zur effizienten Produktion moderner Windkraft-Rotorblätter. Vom Bau der Formen über die Herstellung der Halbschalen und deren Verklebung bis hin zum Finishing der Flügeloberflächen sind sie in allen relevanten Prozessstufen am Werk. Dabei unterstützen sie die Automatisierung, sorgen für den optimalen Materialeinsatz und erhöhen die Sicherheit beim Handling der Kunstharze. Lesen Sie hier, welche Anlagentypen und Systemlösungen des Unternehmens in der Windkraft-Branche derzeit vorrangig zum Einsatz kommen.
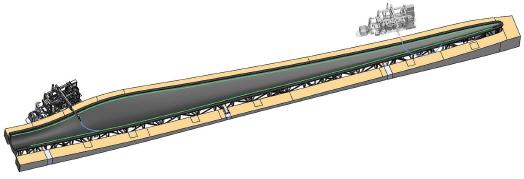
Modifizierte Polyurethane, Epoxidharze und flexible Glasfaserprodukte bestimmen weltweit die Konstruktion und Produktion moderner Windkraft-Rotorblätter für On- und Offshore-Anlagen. Sie werden nicht nur beim Bau der großen Formen und Modelle zur Applikation von Tooling-Pasten und EP-Harzen verwendet sowie für die Herstellung der beiden Flügel-Halbschalen und ihre klebetechnische Verbindung, sondern auch zum Auftragen wetterfester Oberflächenschichten sowie zum Anbringen von Ausgleichsmassen und zahlreiche Feinarbeiten im Rahmen des Finishings.
Für all diese Aufgaben setzen etliche namhafte Hersteller der Windenergie-Branche wie etwa TPI oder Vestas auf die modularen Systemlösungen des deutschen Anlagenbauers TARTLER. Dabei sind es nicht nur die Dosier- und Mischmaschinen der Baureihen Nodopur, Nodopox und Tardosil, die inzwischen in zahlreichen Manufakturen der Rotorblatt-Fertigung zu finden sind. Steigender Nachfrage erfreuen sich auch die innovative Entgasungsstation T-EVAC für Infusionsharze sowie der inzwischen zum Patent angemeldete Vakuum-Fasswechsel von TARTLER, mit dem sich dank der Wiederaufbereitung von reinen Restmengen eine deutliche Abfallreduktion erzielen lässt.
„Häufig ermöglichen unsere Lösungen den Herstellern die Umsetzung wichtiger Maßnahmen zur Prozessoptimierung und Automatisierung. Außerdem unterstützen sie den verlustfreien Materialeinsatz und erhöhen die Sicherheitsstandards beim Umfüllen der Kunstharz-Komponenten aus den Gebinden der Materiallieferanten“, erläutert Firmenchef Udo Tartler.
Grundieren und Auswuchten
Die Applikation der Gel-Coatings auf die Innenflächen der Kavitäten vollziehen viele Rotorblatt-Produzenten mit den 2K-Dosier- und Mischanlagen Nodopur oder Tardosil von TARTLER. Mit diesen Anlagen lassen sich die Grundierungen aus Kieselsäure und angedickten Kunstharzen, die vorrangig dem mechanischen Schutz der Oberflächen und ihrer Versiegelung gegen Feuchtigkeit dienen, sehr homogen und zügig auftragen. Dafür sorgen unter anderem integrierte Volumenstromregelungen, mit denen sich Mischungsverhältnisse und Ausstoßmengen automatisch abstimmen lassen.
Beide Anlagen werden mit SPS von Siemens gesteuert, eignen sich für verschiedene Dosierverhältnisse und lassen sich mit unterschiedlichen Mischköpfen aus dem TARTLER-Sortiment betreiben. Wie ihr Name andeutet, sind die Nodopur-Anlagen prädestiniert für die Verarbeitung von Polyurethan- und Epoxidharzen, während die Tardosil-Maschinen darüber hinaus für Silikone ausgelegt sind.
„Beide Baureihen kommen auch zum Einsatz, wenn zum Auswuchten genau dosierte Ausgleichsmassen in die Rotorblätter eingebracht werden“, ergänzt Udo Tartler.
Vakuuminfusion und Materialentgasung
Für die Vakuum-Direktinfusion, dem von TARTLER entwickelten und zum Patent angemeldeten Verfahren für die Windflügel-Produktion, wird vielerorts die Zwei-Komponenten-Dosier- und Mischanlage Nodopur verwendet. Sie kann bis zu 30 Liter pro Minute ausstoßen, hat eine automatische Vakuum-Nachfülleinheit und eine Siemens-SPS mit Touch-Screen. Für diese Anlagenvariante bietet TARTLER eine Vielzahl verschiedener Mischköpfe an sowie die Option, sie zur Optimierung des Handlings mit einem schwenkbaren Ausleger auszurüsten. Darüber hinaus lässt sich diese Infusionsanlage – wie viele andere Maschinen des Unternehmens auch – mit der Vakuum-Entgasungsstation T-EVAC kombinieren.
„Diese Station dient der prozessintegrierten und sicheren Evakuierung von Luft und Feuchtigkeit aus den Kunstharzen und Härtern – vor dem Dosieren und Mischen“, betont Udo Tartler.
Kleben und Finishen
Nachdem beide Flügelhalbschalen per Vakuuminfusion zu ihrer Form gefunden haben, werden sie passgenau zum fertigen Rotorblatt verklebt. Seit Jahren geschieht dies vielerorts mit den TARTLER-Anlagen der etablierten Baureihe Nodopox, die konzipiert sind für die Verarbeitung und Applikation hochviskoser, pastöser Kunststoffe. Neue Maßstäbe setzt hier seit geraumer Zeit eine Nodopox-Variante, die mit dem integrierten vakuumgestützten Fasswechselsystem TAVA D zur Abfallreduzierung und einem schwenkbaren Mischkopfgalgen mit 5-Meter-Radius (Option) ausgerüstet ist. Diese Anlage verfügt ebenfalls über eine Siemens-SPS mit Touch-Screen und eine Volumenstromregelung. Sie kann mit verschiedenen TARTLER-Mischköpfen arbeiten und bringt bis zu 20 Kilogramm Klebstoff pro Minute aus.
Eine weitere typische „Klebstoffanlage“ von TARTLER ist eine Nodopox, deren Ausstattung auf sogenannte Lightning- und Insert-Anwendungen in der Rotorblatt-Produktion abgestimmt ist. Udo Tartler erklärt: „Dabei kommen Klebstoffe zum Einsatz, die dosiert und vermischt und in geringeren Mengen appliziert werden müssen – beispielsweise zur Befestigung von Blitzableitern oder das Einbringen von Inserts zur Schraubmontage kompletter Flügel.
Diese Anlagen werden sowohl manuell betrieben als auch in Kombination mit Robotern und Handlingeinheiten. Geht es schließlich um das Füllen und Glätten der Klebekanten, so ist es wiederum die eingangs erwähnte Tardosil, mit der sich die dafür verwendeten Putty-Spachtelmassen genau und schnell dosieren, mischen und auftragen lassen. Auch in diesem Fall bietet TARTLER seinen Kunden zahlreiche Möglichkeiten der einsatzspezifischen Anpassung. Dabei bietet das große Repertoire an Modulen viel Freiraum für die optimale anwendungsspezifische Individualisierung der Anlagen.
Individuelle Feinabstimmung
Da TARTLER also in der Lage ist, alle Anlagen sehr genau auf die konkrete Bedarfslage und die Vor-Ort-Situation des Kunden anzupassen, fügen sie sich als maßgeschneiderte Systemlösungen meist nahtlos ein in dessen Produktionslandschaft. Häufig bilden sie hierbei einen wichtigen Leistungsfaktor in den zunehmend automatisierten Abläufen der modernen Rotorblatt-Fertigungslinien.
„Da wir den Herstellern mit unserer vakuumgestützten Fasswechselanlage TAVA D und der Vakuum-Abfüllanlage TAVA F sowie der Flüssigharz-Evakuierungsanlage T-EVAC in der Offline- und Inline-Variante gleich mehrere innovative Schnittstellen-Lösungen zur Verfügung stellen, eröffnen wir viele zusätzliche Möglichkeiten zur Prozessoptimierung und Effizienzsteigerung bei der Verarbeitung und Applikation der Kunstharze“, sagt Udo Tartler.
Mehr Informationen zur Tartler GmbH:
![]() |
TARTLER GmbH |
![]() |
Relystraße 48 |
![]() |
64720 Michelstadt |
![]() |
Tel.: 0049 (0) 60 61 / 96 72-0 |
![]() |
Fax: 0049 (0) 60 61 / 96 72-295 |
![]() |
E-Mail: u.tartler@tartler.com |
![]() |
www.tartler.com |
War dieser Artikel für Sie hilfreich?
![]() |
![]() |
![]() |
![]() |
![]() |
Bitte bewerten Sie diese Seite durch Klick auf die Symbole.
Zugriffe heute: 3 - gesamt: 4406.