Laufende Prozesse optimieren
Eine neue Generation von Werkzeuglösungen
Laut Sandvik Coromant, ist es jetzt an der Zeit, eine neue Wendeschneidplattengeneration für die Drehbearbeitung von ISO P Werkstoffen einzuführen – weil Fertigungsunternehmen damit die besonderen Herausforderungen besser meistern und ihre Produktion effizienter und produktiver gestalten können.
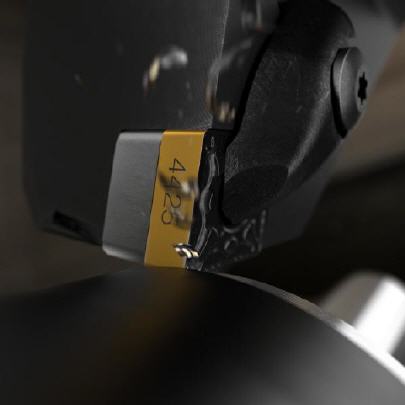
Für Fertigungsunternehmen ist das Abweichen von etablierten Verfahrensweisen mit Risiken verbunden, sei es hinsichtlich eines Produktionsprozesses, der Art der Kommunikation, einer zuverlässigen Maschine oder aber eines bewährten Werkzeuges. Kein Wunder also, dass es verlockend ist, hier dem Sprichwort „Never change a running system“ zu folgen – schließlich könnten ein neues Werkzeug oder ein digitalisierter Prozess mehr Probleme als Vorteile mit sich bringen. Doch auch wenn es kurzfristig vorteilhafter scheint, alles beim Alten zu belassen, sind Fertigungsunternehmen heute mehr denn je gefordert, mit der Zeit zu gehen – ganz gleich, ob sie in Groß- oder in Kleinserie produzieren.
Warum gerade jetzt, das hat eine Studie der internationalen Wirtschaftskanzlei Pinsent Masons untersucht. Ihre Umfrage unter 100 Fertigungsunternehmen und Studenten in Deutschland hat drei Haupttreiber für Veränderungen identifiziert.
Erstens lösen disruptive Industrie 4.0-Technologien wie künstliche Intelligenz (KI) und intelligente Automatisierung eine neue industrielle Revolution aus. Zweitens treibt die grüne Agenda die Fertigungsunternehmen schneller zu Geschäftsmodellen mit geringerem CO2-Ausstoß. Drittens wird makroökonomischer Druck infolge des Brexits und der Covid-19-Pandemie zu einer Fragmentierung der globalen Lieferketten führen.
Wie also können Fertigungsunternehmen diese Hindernisse überwinden, ohne die beiden wichtigsten Herausforderungen aus den Augen zu verlieren: die Steigerung der Produktionsleistung und die Reduzierung der Kosten? Und wie kann das auch bei der ebenso häufigen wie komplexen Bearbeitung von ISO P Werkstoffen gelingen? Die Antwort: Möglich macht dies die neue Sortengeneration, mit der laufende Prozesse optimiert werden können.
Das richtige Material
Steigerung der Produktionsleistung und Reduzierung der Kosten – darauf kommt es auch bei profitablem Stahldrehen an. In welchem Maß sich Produktionskosten senken lassen, hängt nicht zuletzt von der spezifischen Situation des jeweiligen Fertigungsunternehmen ab. Zum Beispiel davon, ob dieses in Groß- oder Kleinserien fertigt. In der aktuellen Covid-19-Krise sind Produktionsbetriebe zudem mit wechselnden und unvorhersehbaren Szenarien hoher oder niedriger Nachfrage konfrontiert, an die sie sich entsprechend anpassen müssen.
Grundsätzlich müssen Fertigungsunternehmen immer danach streben, ihre Bearbeitungsleistung zu maximieren. Nach den Erkenntnissen von Sandvik Coromant kann das die Gesamtkosten pro Bauteil um 15 Prozent senken. Um eine höhere Produktionsleistung zu realisieren, ist es außerdem notwendig, die Zerspanungsraten zu erhöhen. Für die Fertigung von mehr Stahlkomponenten in kürzerer Zeit müssen zudem die Ausschussquote und die Bauteilbeschädigungen reduziert werden.
Zum Erreichen dieser Ziele ist die Wahl des Werkzeugs von zentraler Bedeutung, insbesondere die Wahl der Wendeschneidplatte. Sandvik Coromant rät zu Wendeschneidplatten, die beim Stahldrehen eine möglichst vorhersagbare und konstante Leistung liefern.
In Form bleiben
Sandvik Coromant hat deshalb sein bestehendes Sortiment um zwei leistungsstarke Hartmetallwendeschneidplattensorten erweitert: GC4415 und GC4425. Die Bezeichnungen der Wendeschneidplatten beziehen sich auf die ISO-Bereiche P15 und P25, also die Anforderungen, die unterschiedliche Arbeitsbedingungen an die Bearbeitungsparameter stellen: Schnittdaten, Oberflächengüte, Schnitttiefe, bearbeitete oder raue Oberflächen, kontinuierliche oder unterbrochene Schnitte.
Die beiden neuen Hartmetallwendeschneidplattensorten erfüllen genau diese Anforderungen: GC4425 bietet eine verbesserte Verschleißfestigkeit, Temperaturbeständigkeit und Zähigkeit. GC4415 wurde als Ergänzung dazu entwickelt, wenn eine höhere Leistung und eine bessere Temperaturbeständigkeit erforderlich sind.
Beide verfügen über die Inveio-Technologie der zweiten Generation. Dessen Einzigartigkeit zeigt sich, wenn man das Material auf mikroskopischer Ebene untersucht: Die Oberfläche ist durch eine unidirektionalen Kristallorientierung charakterisiert. Jeder Kristall ist in der gleichen Richtung gereiht, was eine starke Barriere zur Spanbildungszone schafft und die Widerstandsfähigkeit gegen Freiflächen- und Kolkverschleiß verbessert. Außerdem wird die Wärme schneller aus der Spanbildungszone abgeführt, wodurch die Schneidkante länger intakt bleibt.
Dank der innovativen Inveio Technologie können GC4415 und GC4425 eine größere Anzahl von Werkstücken bearbeiten. Jede Wendeschneidplatte trägt zu einer verlängerten Werkzeugstandzeit bei, verhindert plötzlichen Werkzeugbruch und reduziert Nacharbeit und Ausschuss.
Mit der Möglichkeit, mehr Bauteile in einer Aufspannung zu bearbeiten, können die neuen Wendeschneidplattensorten solche Produktionsunterbrechungen reduzieren, die durch die größten Zeitfresser in der modernen Fertigung verursacht werden: häufige Wendeschneidplattenwechsel und den Zeitaufwand für die Suche nach der richtigen Wendeschneidplatte für die jeweilige Anwendung und das jeweilige Material.
Weitere Optimierungen
Darüber hinaus kann der Einsatz von Kühlmittel die Leistung der Wendeschneidplatte in jeder Hinsicht weiter verbessern und entscheidend zur Senkung der Gesamtproduktionskosten beitragen. Die gezielte Kühlung von unten reduziert die Hitze in der Schneidzone, wodurch verbesserte Standzeiten und vorhersagbare Zerspanungsprozesse möglich werden. Derart kann der Maschinenbediener die Schnittgeschwindigkeit oder den Vorschub erhöhen, was wiederum die Produktivität steigert und den Ausstoß maximiert.
Mithilfe einer Präzisionskühlung mit festen Düsenpositionen gelangt das Kühlmittel direkt in die Schneidzone – eine gute Möglichkeit zur erfolgreichen Spankontrolle. Bei korrekter Anwendung erhöht der gezielte Kühlmitteleinsatz den Output, die Prozesssicherheit, die Werkzeugleistung und die Bauteilqualität. Dies alles sind wichtige Eckpfeiler einer erfolgreichen Bearbeitung.
Das richtige Werkzeug und ein geeigneter Kühlmitteleinsatz bringen klare Vorteile bei der Bearbeitung. Doch was können Fertigungsunternehmen durch den Einsatz eines neuen Bearbeitungsverfahrens im Bereich der Stahldrehoperationen gewinnen? Beispielsweise durch den Einsatz von PrimeTurning™, einem Verfahren für die Großserienfertigung oder für Komponenten, bei deren Bearbeitung mehrere Set-ups und häufige Werkzeugwechsel gefordert sind.
Immer dann, wenn die Drehbearbeitung zum Flaschenhals im Produktionsprozess wird, können pro Durchlauf weniger Bauteile gefertigt werden. Daher müssen Fertigungsunternehmen ihren Drehprozess überdenken, um die maximale Leistung aus ihren Werkzeugmaschinen herauszuholen. Hier kann PrimeTurning unterstützen, indem es Drehbearbeitungen in alle Richtungen ermöglicht. Auf diese Weise können Fertigungsunternehmen ihre Produktivität gleich mehrfach steigern, ohne Kompromisse bei Prozesssicherheit und Werkzeugstandzeiten einzugehen. Denn diese Art des Drehens erweist sich im Vergleich zum konventionellen Drehen als wesentlich effizienter und produktiver.
Positive Veränderung
Seit ihrer Markteinführung haben die Hartmetallwendeschneidplatten GC4415 und GC4425 ihre Vorteile bereits vielfach bewiesen. In einem Fall hat ein Maschinenbauunternehmen die Wendeschneidplatte GC4415 im Vergleich mit einer Wettbewerbslösung eingesetzt, und zwar bei der Bearbeitung eines Werkstücks aus CMC 02.1-Stahl mit einer Brinell-Härte von 220 HB.
Bei der axialen Außendreh- und leichten Schruppbearbeitung erzielte der Kunde mit der GC4415 eine Schnittgeschwindigkeit (vc) von 300 m/min und einen Vorschub (fn) von 0,33 mm/U. Die Wendeschneidplatte des Wettbewerbers erreichte dagegen lediglich eine Schnittgeschwindigkeit von 250 m/min und einem Vorschub von 0,25 mm/U. Sie bearbeitete 200 Stück pro Schneidkante, bevor sie getauscht werden musste, während mit GC4415 256 Stück zerspant werden konnten und sie lediglich erste Verschleißmerkmale zeigte. Durch den Wechsel zur GC4415 und die Erhöhung der Schnittdaten konnte der Kunde seine Produktivität um 210 Prozent steigern und die Kosten um 53 Prozent senken.
Mehr Informationen zu Sandvik Tooling Deutschland:
![]() |
Sandvik Tooling Deutschland GmbH |
![]() |
Geschäftsbereich Coromant |
![]() |
Heerdter Landstraße 243 |
![]() |
40549 Düsseldorf |
![]() |
Tel. +49 211 5027-0 |
![]() |
Fax +49 211 5027-500 |
![]() |
E-Mail: de.coromant@sandvik.com |
![]() |
www.sandvik.coromant.com/de |
War dieser Artikel für Sie hilfreich?
![]() |
![]() |
![]() |
![]() |
![]() |
Bitte bewerten Sie diese Seite durch Klick auf die Symbole.
Zugriffe heute: 3 - gesamt: 4409.