Stahl im Zeitalter der e-Mobilität
Ein Werkstoff mit vielen Vorteilen
Mobilität ohne CO2-Emissionen – das klingt verlockend. Deshalb haben sich Viele Elektromobilität auf die Fahnen geschrieben, von der Bundesregierung über Automobilhersteller und Zulieferer bis hin zu Stromerzeugern und Stadtwerken. Aber noch sind zahlreiche Fragen offen. Wird unsere zukünftige Mobilität so aussehen, wie sie in zahlreichen Szenarien vorgestellt wird? Und können wir sie uns leisten?
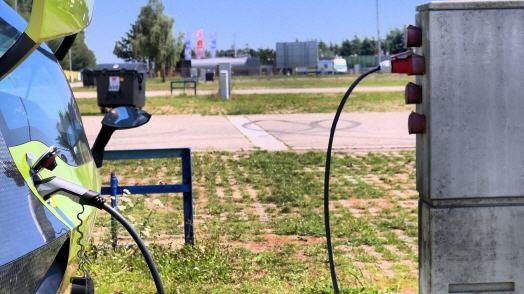
Bei den Zweirädern sind sie inzwischen ein Renner, die elektrisch angetriebenen E-Bikes und E-Roller. Bei Personenwagen noch nicht: Nur rund 140 000 rein elektrisch betriebene Autos fahren derzeit auf deutschen Straßen. Wenn es nach dem Willen der Bundesregierung ginge, sollten es seit dem Jahr 2020 eigentlich schon eine Million sein.
Größtes Hindernis für eine schnelle Verbreitung elektrisch angetriebener Fahrzeuge ist bisher die Batterie: Sie ist schwer, teuer und ermöglicht gegenüber konventionellen Antrieben nur eine geringe Reichweite. Bei Elektroautos steckt die Kraft im Akku. Lithium-Ionen-Zellen, die zu einem Akku zusammengeschaltet und meist im Fahrzeugboden untergebracht werden, ermöglichen heute je nach Fahrbedingungen Reichweiten von 120 bis 632 Kilometer.
Statistisch fahren die Deutschen nicht mehr als 40 Kilometer am Tag und parken länger als vier Stunden an einer Stelle – ideale Voraussetzungen für den Einsatz von Elektromobilen und das Aufladen der Akkus. Experten gehen deshalb davon aus, dass der Einsatzschwerpunkt solcher Fahrzeuge in den Städten liegen wird. Wie schnell sich Elektroautos in Zukunft durchsetzen werden, hängt im Wesentlichen von der Ladekapazität der Speicherelemente und der Entwicklung ihrer Kosten ab.
Heute in kleinen Serien hergestellt, liegt ihr Preis noch über 500 Euro je Kilowattstunde. Eine Batterie mit einem Energieinhalt von 30 Kilowattstunden, die eine Reichweite von rund 200 Kilometer möglich macht, kostet dementsprechend mehr als 15 000 Euro. In großen Serien produziert, könnte ihr Stückpreis allerdings auf knapp die Hälfte sinken.
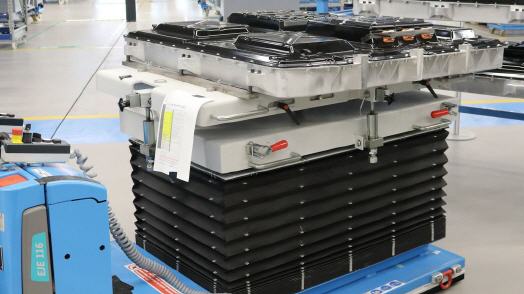
Erhebliches Mehrgewicht
Auch das Gewicht der Batterien ist eine große Herausforderung: Zwischen 250 und 750 Kilogramm wiegen sie zurzeit. Trotz Wegfall von Verbrennungsmotor und Getriebe sowie anderer Komponenten im Antriebsstrang macht der Wechsel von konventionellem zu elektrischem Antrieb solche Autos letztendlich um mehr als 200 Kilogramm schwerer. Da dieses Gewicht die Reichweite deutlich reduziert, sind Leichtbaumaßnahmen unumgänglich.
Diskutiert wird vor allem der intensive Einsatz von Werkstoffen wie Aluminium und faserverstärkten Kunststoffen. Doch der Einsatz dieser Werkstoffe ist nicht zum Nulltarif zu haben. Dies liegt nicht nur an den höheren Kosten für diese Materialien, auch deren Verarbeitung ist teilweise überaus aufwendig. Längere Taktzeiten bei der Herstellung führen zu niedrigeren Produktionszahlen und verlangen Investitionen in parallele Fertigungsketten.
So bedeutet bereits der moderate Einsatz von Faserverbundwerkstoffen in der Karosserie erhebliche Mehrkosten. In der gewichtsoptimierten Karosserie in Mischbauweise der Studie ›Superlight-Car‹, die einen Materialmix von 53 Prozent Aluminium, 36 Prozent Stahl, sieben Prozent Magnesium und vier Prozent Faserverbund-Kunststoffen aufweist, summieren sich die Mehrkosten durch teurere Werkstoffe und aufwendigere Fertigungsprozesse auf rund 780 Euro pro Karosserie. Das ist für eine Gewichtsreduktion von 35 Prozent oder rund 100 Kilogramm sehr viel. Damit wirkt neben der Batterietechnik der Leichtbau als weiterer Kostentreiber.
Wenn sich Fahrzeuge mit Elektroantrieb jedoch flächendeckend durchsetzen sollen, müssen sie für die Verbraucher erschwinglich sein. Die meisten Automobilhersteller setzen bei der Karosserie auf Stahl – und das aus gutem Grund. Durch sein einzigartiges Eigenschaftsprofil hat sich der Werkstoff im Automobilbau mit kostengünstigem Leichtbau über Jahrzehnte bewährt.
Für welche Lösungen sich Stahl im Hinblick auf die Elektromobilität empfiehlt, wurde auch im Projekt ›Future Steel Vehicle‹ von WorldAutoSteel, einer Organisation des Weltstahlverbandes ›worldsteel‹, untersucht. Die Ergebnisse zeigten, dass Bauteile aus Stahl bei umfassender Betrachtung von Gewicht, Kosten und CO2-Emissionen vorteilhafter als Bauteile aus anderen Metallen sind.
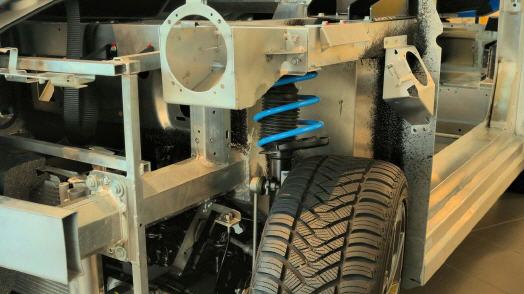
Recycling ohne Qualitätsverlust
Gerade die ganzheitliche Berücksichtigung von Materialerzeugung, Bauteilherstellung und Recycling im Rahmen ökologischer Betrachtungen ist bei Elektrofahrzeugen noch wichtiger als bisher, da sich diese durch die deutlich geringeren CO2-Emissionen während der Nutzungsphase stärker auswirken. Hier spielt Stahl seine Vorzüge aus. So erfordert die Herstellung eines Karosserieblechs aus hochfestem Stahl lediglich ein Viertel der Energiemenge, die beispielsweise für ein funktionsgleiches Aluminiumblech benötigt wird. Und auch beim Recycling, das bei vielen Verbundwerkstoffen in der großtechnischen Anwendung nicht funktioniert, punktet der Werkstoff Stahl. Schließlich lässt er sich nahezu vollständig und beliebig oft ohne Qualitätsverlust recyceln.
Die genannten Vorteile bei Gewicht, Kosten und CO2-Emissionen zeigen sich auch beim Blick auf die E-Fahrzeugkonzepte der Automobilhersteller. Der Mini E und der Active E von BMW sowie die A-Klasse E-Cell von Mercedes Benz ähneln in der Karosseriestruktur stark ihren konventionell angetriebenen Geschwistern. Die Herstellung unterscheidet sich lediglich dadurch, dass die E-Autos an einem bestimmten Punkt der Produktion aus der Linie gesteuert werden, um ihren E-Antrieb zu erhalten. Danach werden sie wieder in den Produktionsablauf eingeschleust. Das spart Kosten und unterstützt nachhaltiges Wirtschaften mit Rohstoffen.
Die Karosseriestrukturen zukünftiger Modellgenerationen werden im Vergleich zu gegenwärtigen Konzepten stärker an die Anforderungen elektrobetriebener Fahrzeuge angepasst. Stahl wird hier nach wie vor eine entscheidende Rolle spielen. So bestehen Bestrebungen, die stabilen Gehäuse aus Stahlblech, die die Batterien bei Unfällen schützen und das Austreten der Elektrolyte verhindern, als tragende Elemente in die Karosseriestruktur zu integrieren. Im Falle eines Seitenaufpralls verhindern sie damit auch die Deformation der Fahrgastzelle und schützen die Insassen.
Doch nicht nur in der Karosserie, auch beim elektrifizierten Antrieb zählt Stahl in Form von so genannten ›nichtkornorientierten Elektroblechen‹ zu den notwendigen Grundwerkstoffen. Speziell für hocheffiziente Elektromotoren entwickelte Stahlsorten ermöglichen einen verbesserten Wirkungsgrad bei erhöhter Drehzahlfestigkeit und Temperaturbeständigkeit.
Wichtige Fragen beziehen sich auch auf die Infrastruktur. Erst mit der Errichtung von Tankstellennetzen in den 20er Jahren des letzten Jahrhunderts und dem überall verfügbaren Angebot an preiswertem Treibstoff verbreitete sich das Automobil. Elektrofahrzeuge benötigen eine auf sie zugeschnittene Infrastruktur. Internationale Standards müssen zügig festgelegt werden, wenn die Forderung nach breiter Einführung von Elektroautos schnell umgesetzt werden soll.
International normierte Stecker, Kupplungen, Ladestationen und Abrechnungssysteme würden die Durchsetzung fördern. Weiterhin ist unklar, inwieweit die Kunden bereit sind, auf Komfort zu verzichten. Denn auch Heizung und Klimaanlage, elektrische Fensterheber und Sitzverstellung, beheizbare Außenspiegel, Radio- und Navigationssysteme verbrauchen Strom und reduzieren die Reichweite.
Trotz allem ist bereits jetzt die Bereitschaft groß, dem Umweltschutz zuliebe auf Elektroantriebe umzustellen. Elektrofahrzeuge entlasten unser Klima jedoch erst dann wirksam, wenn sie mit CO2-armem Strom betrieben werden. Eine kostengünstige Großserienproduktion ist hierfür die Voraussetzung. Zudem sollen Herstellung, Nutzung und Recycling der Fahrzeuge nachhaltig sein. Stahl ist als preiswerter, nachhaltiger und vielseitig einsetzbarer Automobilwerkstoff in all diesen Disziplinen vorbildlich.
Download
Diesen Artikel finden Sie auch in Heft 5/2021 auf Seite 90. Zum besagten Heft führt ein Klick auf den nachfolgenden Button!
Mehr Informationen zum Stahl-Informations-Zentrum:
![]() |
Stahl-Informations-Zentrum |
![]() |
Sohnstraße 65 |
![]() |
40237 Düsseldorf |
![]() |
Tel.: +49 (0)211 6707-967 |
![]() |
Fax: +49 (0)211 6707-344 |
![]() |
E-Mail: siz@stahl-info.de |
![]() |
www.stahl-info.de |
War dieser Artikel für Sie hilfreich?
![]() |
![]() |
![]() |
![]() |
![]() |
Bitte bewerten Sie diese Seite durch Klick auf die Symbole.
Zugriffe heute: 3 - gesamt: 3789.