Das Eckige muss rund werden
Sprödes Material stellt Herausforderungen
Batterien mit möglichst viel Energie sind vor allem für Elektrofahrzeuge gefragt. Das Fraunhofer IPA arbeitet an Festkörperbatterien, die mit 700 Wattstunden pro Kilogramm eine fast doppelt so große Energiedichte haben sollen wie heutige Lithium-Ionen-Batterien. Digitale Zwillinge sollen helfen, bestehende Hürden für die Massenproduktion aus dem Weg zu räumen.
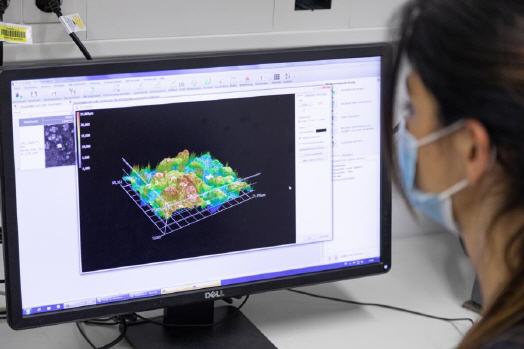
Beim Fraunhofer-Institut für Produktionstechnik und Automatisierung IPA konzentriert man sich auf Technologien, bei denen das Upscaling vom Labormuster zur industriellen Großproduktion machbar erscheint. Entscheidend dafür ist, dass sich neuartige Batterien mit gewissen Modifikationen auch auf bestehenden Anlagen produzieren lassen. Als Endprodukt sollen dabei Rundzellen im gängigen Format 21700 vom Band rollen, die einen Durchmesser von 21 Millimetern haben und 70 Millimeter lang sind.
Hersteller wie die VARTA AG, ein Projektpartner des Fraunhofer IPA für die Batterieforschung, haben sich nicht ohne Grund mit ihren Anlagen auf diese zylindrischen Zellen festgelegt. Einzelne solcher Zellen lassen sich in einem Batteriemodul leichter überprüfen und bei einem möglichen Defekt austauschen. Über Hohlräume zwischen den Zellen kann Wärme abgeführt werden. Oft werden die Zellen noch als Energieträger in anderen Anwendungen weiter genutzt, nachdem die Autobatterie ausgemustert wurde. Standardisierte Rundzellen machen das leichter.
Festkörperbatteriezellen enthalten im Gegensatz zu einer Lithium-Ionen-Batterie keine Flüssigkeit als Elektrolyt, sondern einen keramischen oder sulfidischen, also schwefelhaltigen, Festkörperelektrolyt. Auch Polymerelektrolyte sind eine Option, allerdings erfordern sie höhere Betriebstemperaturen von über 60 Grad Celsius. Die Zellen sind heute meist als flache, rechteckige Pouchzellen aufgebaut. Aktuelle Entwicklungen im Bereich der keramischen Festkörperelektrolyte am Fraunhofer IPA zielen darauf ab, den Sinterprozess für das Keramikmaterial zu beschleunigen und schon in diesem Schritt die gewünschte Geometrie für den späteren Einsatz in der Batterie herzustellen. Die Sprödigkeit des Materials macht dabei allerdings die Nachbearbeitung und das Wickeln zu einer Rundzelle schwierig.
Für den Einsatz in Rundzellen bieten die sulfidischen Festkörperelektrolyte einen entscheidenden Vorteil. Bei der richtigen Verarbeitung können flexible Schichten hergestellt werden, die auch bei geringen Wickelradien stabil sind. Hinzu kommt, dass die sogenannte Thio-LISICON-Sulfid-Familie, anorganische Elektrolyte, vielversprechende Ergebnisse für die ionische Leitfähigkeit bei niedrigen Temperaturen zeigt. Doch obwohl sulfidische Elektrolyte ausgezeichnete Ionenleitfähigkeiten aufweisen und somit mit organischen Flüssigelektrolyten konkurrieren könnten, sind sie im Moment viel teurer. Durch den Aufbau entsprechender Produktionskapazitäten kann eine kostengünstige Herstellung der sulfidbasierten Elektrolyte realisiert werden.
Bis zur industriellen Fertigung von Festkörperbatterien ist es noch ein weiter Weg. So werden Festkörperbatterien heutzutage überwiegend mit Lithium als Anode aufgebaut, was besondere Herausforderungen an die Montageumgebung mit sich bringt. Damit das Material nicht mit dem Sauerstoff oder der Feuchtigkeit aus der Luft reagiert, sind neben einer kostspieligen Trockenraumbedingung teils sogar zusätzliche gekapselte Produktionsbereiche mit einem Schutzgas wie Argon notwendig.
Forscherinnen und Forscher vom Fraunhofer IPA untersuchen deshalb, wie Festkörperbatterien unter moderaten Bedingungen gefertigt werden können. »Ein vielversprechender Ansatz ist dabei die In-situ-Abscheidung des Lithiummetalls. Dabei bilden die in der Kathode vorhandenen Lithium-Ionen beim ersten Ladevorgang eine Schicht auf dem Ableiter der negativen Elektrode«, sagt Duygu Kaus vom Zentrum für Digitalisierte Batteriezellenproduktion (ZDB). Versuchsreihen sollen zeigen, mit welchem Ableitermaterial die In-situ-Anodenbildung am besten gelingt.
Um herauszufinden, welche der vielen Parameter für die Fertigung am geeignetsten sind, ist es bisher erforderlich umfangreiche Versuchsreihen durchzuführen – und zwar nicht nur im Labor, sondern auch unter skalierbaren industriellen Produktionsbedingungen. Der Materialverbrauch wäre dabei erheblich und jede Modifikation würde sich auf weitere Schritte in der Prozesskette auswirken.
»Eine elegantere Lösung ist der Digitale Zwilling. Er assis- tiert der Mitarbeiterin oder dem Mitarbeiter in der Produktion mit Hilfe seiner Überwachungs-, Analyse- und Vorhersagefähigkeiten«, sagt Soumya Singh vom ZDB. Beim Digitalen Zwilling handelt es sich um ein virtuelles Abbild einzelner Prozessschritte oder ganzer Fertigungslinien, das kontinuierlich mit zusätzlichen Betriebsdaten angereichert wird. Der Digitale Zwilling unterstützt Ingenieure dabei, das zukünftige Verhalten der Fertigung bei verschiedenen Parametrierungen zu simulieren und deren Auswirkungen im Voraus zu bewerten.
Gefüttert mit umfangreichen Datenquellen aus der Produktion, trifft der Digitale Zwilling Aussagen über die Effizienz einzelner Prozessschritte, aber auch über die Auswirkungen unterschiedlicher Verarbeitungsparameter auf die zu erreichende Qualität der Zwischenprodukte, Prozesszeiten und deren Stabilität. So lässt sich mit dem Digitalen Zwilling beispielsweise auf dem Computer des Bedieners bestimmen, wie die Bearbeitungsschritte für eine Elektrode aussehen müssten, damit sie am Ende elastisch genug ist, um sich wickeln zu lassen.
Nach der Implementierung ist der Digitale Zwilling mit dem Produktionsschritt synchronisiert und wird kontinuierlich mit aktuellen Daten aus der Fertigung gespeist. Er überwacht nun, wie stabil die Produktion läuft und wird zum integralen Bestandteil des Qualitätsmanagements.
Mehr Informationen zum Fraunhofer IPA:
![]() |
Fraunhofer-Institut für Produktionstechnik und Automatisierung IPA |
![]() |
Nobelstrasse 12 |
![]() |
70569 Stuttgart |
![]() |
Telefon: +49 711 970-00 |
![]() |
Telefax (Zentrale) +49 711 970-1399 |
![]() |
www.ipa.fraunhofer.de |
War dieser Artikel für Sie hilfreich?
![]() |
![]() |
![]() |
![]() |
![]() |
Bitte bewerten Sie diese Seite durch Klick auf die Symbole.
Zugriffe heute: 2 - gesamt: 3967.