Individuelle Pneumatik für die Schrumpftechnik
SMC kombiniert Druckschalter, Filter und Ventile
Anspruchsvolle Branchen wie die Präzisionsfertigung, der Maschinenbau, die Luft- und Raumfahrtindustrie oder die Medizintechnik benötigen genaueste Werkzeugaufnahmen, die auch bei hohen Drehzahlen beste Fertigungsergebnisse garantieren. Für das zuverlässige Verbinden von Werkzeugaufnahme und Werkzeug nutzen die Maschinenbauer von Diebold deshalb eine ausgefeilte thermische Schrumpftechnologie. Ihre neue, automatische Kühlstation sorgt dabei für mehr Sicherheit und Genauigkeit. Aber wie kommt die Kühlflüssigkeit ins Kühlrohr und wie wird die Werkzeugaufnahme trocken geblasen? Die Lösung: Ein komplettes Pneumatik-Panel von SMC.
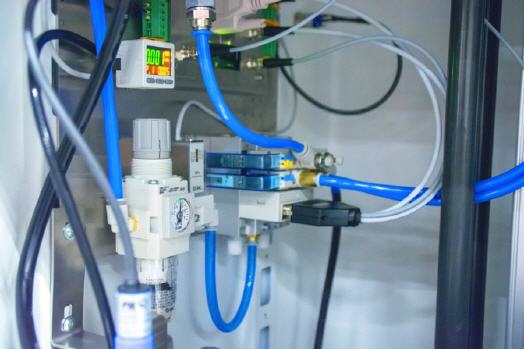
Unterschiedliche Materialien und Fertigungsprozesse benötigen unterschiedliche Bohr- und Fräswerkzeuge. Diese müssen sich deshalb schnell und prozesssicher tauschen lassen. Zugleich müssen sie aber auch möglichst fest in ihrer Aufnahme sitzen – bei möglichst gutem Rundlauf und damit auch geringster Unwucht. Das ist besonders bei hohen Drehzahlen wichtig. Anwendungen wie beispielsweise die Komponentenfertigung für Luft- und Raumfahrt haben enorm geringe Toleranzen – was besondere Ansprüche an die Präzision ihrer Werkzeuge stellt.
Die Schrumpftechnik-Experten bei Diebold entwickeln dafür seit Jahrzehnten leistungsstarke thermische Schrumpfgeräte, die das Fügen der Werkzeuge in die Werkzeugaufnahme ermöglichen. Um die durch den Prozess erhitzten Werkzeugaufnahmen und Werkzeuge schonend zu kühlen, hat Diebold jetzt den innovativen TubeChiller® entwickelt. Eine komplett mit den passenden Ventilen, Filter-Reglern und Druckschaltern konfektionierte pneumatische Baugruppe von SMC reduziert die Montagezeit und sorgt für den nötigen Wasser- und Luftdruck.
Die Helmut Diebold GmbH & Co. wurde im Jahr 1952 als Lohnfertiger gegründet. Mit großem Erfolg: Das 1968 eröffnete Junginger Fabrikgebäude wurde für die Fertigung von Werkzeughaltern und Präzisionsspindeln konzipiert und wurde seitdem stetig erweitert. Heute beherbergt es modernste Anlagen in einer vollklimatisierten Fertigung, an denen mehr als 120 Experten Spannwerkzeuge, Spindeln sowie die passende Mess- und Schrumpftechnik herstellen. Kompetenter Service für die ausgelieferten Produkte und Schrumpfmaschinen versteht sich dabei von selbst. Wenn gewünscht, produziert Diebold zudem weiter als Lohnfertiger individuelle Komponenten für seine Kunden.
Fräs- und Bohrwerkzeuge optimal festhalten
Heimwerker kennen das Problem: Ist der Bohreinsatz nicht ordentlich ins Futter eingespannt, wird das Loch im besten Fall krumm und im schlimmsten muss man einen neuen Bohrer kaufen. „In der Hausanwendung und oft auch in der Industrie werden Bohr- und Fräswerkzeuge manuell in das Futter gespannt“, sagt Markus Hellstern, Projektleiter bei Diebold. „So lassen sich die Werkzeuge schnell wechseln, für höchste Genauigkeitsansprüche ist diese Methode aber nicht geeignet.“
Branchen wie die Medizintechnik benötigen teils sehr lange und feine Werkzeuge, die sich auch bei hohen Drehzahlen nicht in ihrer Werkzeugaufnahme lösen dürfen. Die Experten von Diebold nutzen deshalb das induktive Schrumpfen für diese anspruchsvollen Anwendungen. Markus Hellstern: „Bei dieser Methode wird die Werkzeugaufnahme innerhalb von wenigen Sekunden auf über 300 Grad erhitzt. Dadurch weitet sich die Bohrung der Werkzeugaufnahme elastisch aus und das Werkzeug kann eingefügt werden. Beim Abkühlen schrumpft die Bohrung wieder und die Werkzeugaufnahme mit Werkzeug ist für das prozesssichere Zerspanen einsatzbereit.“
Der Prozess ist beliebig oft wiederholbar, falls das Werkzeug gewechselt werden muss. Dabei darf die Werkzeugaufnahme aber nicht überhitzt werden sonst leidet ihre Lebensdauer und die Funktionssicherheit. Derart heiße Komponenten stellen zudem ein Sicherheitsrisiko für Bediener da, Werkzeugaufnahme und Werkzeug müssen entweder lange selbst durch Raumluft abkühlen oder anders gekühlt werden.
„Das ist eine Herausforderung. Würde die Komponente ungleichmäßig und nur punktuell gekühlt, könnte sie sich verziehen und die Genauigkeit des Werkzeugs stark beeinträchtigen“, erläutert Markus Hellstern. Für seine neueste Schrumpfgeräte-Generation der Serie US 1100 hat Diebold deshalb den TubeChiller® entwickelt. Er kühlt nicht nur effektiv und schonend, sondern schützt mit seiner Bauweise die Bediener.
Der Clou: Nach dem Schrumpfvorgang fährt ein durchsichtiges Kühlrohr (Tube) automatisch über die Werkzeugaufnahme. Druckluft presst dann die Kühlflüssigkeit von unten in das Kühlrohr und wälzt die Kühlflüssigkeit während des kompletten Prozesses um. So kühlt sie die Komponente gleichmäßig.
Das System ist unabhängig von Kontur oder Gewicht der eingesetzten Werkzeugaufnahme und bietet darüber hinaus zweifache Sicherheit für Bediener. Es überwacht den Prozess sensorisch und erlaubt zudem eine visuelle Prüfung durch seine transparente Röhre. Druckluftdüsen trocknen schließlich die Werkzeugaufnahme, während die Röhre wieder einfährt und die Entnahme des sofort einsetzbaren Bohr- oder Fräswerkzeugs erlaubt.
Kühlflüssigkeit pumpen, Werkzeugaufnahme sicher trocknen
Für einen reibungslosen Ablauf der Kühlung und Trocknung im Schrumpfgerät von Diebold muss immer genug Druckluft anliegen. Die entsprechenden Filter-Regler-Einheiten, Ventile und Druckschalter müssen langlebig, leicht zu warten und für spezifische Kundenanforderungen konfigurierbar sein. Zudem benötigt die schonende Kühlung der Werkzeugaufnahmen besonders reine Luft – die Toleranzen gegenüber Verunreinigungen am Werkzeug sind minimal.
„Das pneumatische System für komplexe Maschinen besteht aus diversen Komponenten, die optimal aufeinander abgestimmt sein müssen“, sagt Florian Auch, Sales Engineer bei SMC. „Je vielfältiger und zahlreicher die Komponenten, desto größer wird die Herausforderung und der Aufwand für die Maschinenbauer.“ Sie müssen die Anlage und all ihre Bauteile effizient auslegen – das kostet viel Zeit. SMC vereint deshalb alle wichtigen Komponenten zur Steuerung und Reinigung der Druckluft auf einer Metallplatte, die komplett konfektioniert geliefert wird und damit Zeit und Ressourcen spart.
Bevor die Druckluft im System verwendet wird, befreit sie ein Filter-Regler der Serie AW20 von allen Verunreinigungen. Wo die Druckluft hinkommt, kontrolliert eine Ventilinsel der Serie SY5000 mit einem 5/3-Wege-Ventil und einem monostabilen 5/2-Wege-Ventil. Sie teilen sich mehrere Aufgaben: Das 5/2-Wege-Ventil führt die Luft zu einem Zylinder, der das Rohr des TubeChiller® über die Werkzeugaufnahme fährt. Das 5/3-Wege-Ventil versorgt einen Tank mit Druckluft, die die Kühlflüssigkeit in das Rohr presst. Zudem versorgt das Ventil den Düsenring mit Druckluft, der die Werkzeugaufnahme nach dem Kühlprozess abtrocknet.
Ein Druckschalter der Serie ISE10E behält den Gesamt-Systemdruck im Blick, während ein digitaler ISE20-Druckschalter den Druckaufbau im Tank überwacht. Florian Auch: „Die optimalen Werte im Tank können dem digitalen Druckschalter via Druckluft praktisch ‚beigebracht‘ oder auch schon im Vorhinein über dessen 7-Segment-Anzeige einprogrammiert werden. Das spart Zeit und Aufwand.“ Die Kommunikation mit der übergeordneten Steuerung funktioniert über einen 25-poligen D-Sub-Stecker.
„Die Platten mit den kundenindividuell zusammengestellten Komponenten werden fertig konstruiert und geprüft von uns geliefert“, erläutert Florian Auch. So müssen die Maschinenbau-Experten bei Diebold sie nur noch in ihre Schrumpfgeräte integrieren, anschließen und mit den gewünschten Druckwerten programmieren. Der Montageprozess wird damit deutlich schneller und effizienter. Alle verwendeten Bauteile zeichnen sich durch hohe Robustheit und eine lange Lebensdauer aus. Zudem bietet die räumlich optimierte Anordnung der Komponenten weitere Vorteile: Das Risiko von Leckagen ist minimiert und es wird insgesamt weniger Druckluft benötigt.
Optimal konstruiertes Komponentenpaket auf einer Platte
Im Dauertest bei Diebold und in den ersten Kundenmaschinen haben sich die Komponenten bestens bewährt. „Besonders der digitale Druckschalter von SMC hat uns überzeugt“, sagt Markus Hellstern. „Seine umfangreiche Funktionalität und hohe Zuverlässigkeit erspart uns bei jedem Schrumpfgerät Aufwand und Montagezeit.“ Auch die Schnelligkeit bei der Umsetzung der hohen Anforderungen an alle Komponenten und das Paket als Ganzes weiß zu beeindrucken. Markus Hellstern: „Zusammenfassend würde ich es noch einmal exakt genauso machen.“
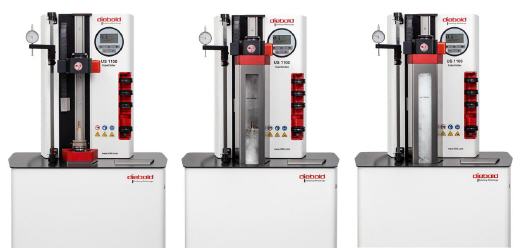
Mehr Informationen zur SMC Pneumatik GmbH:
![]() |
SMC Pneumatik GmbH |
![]() |
Boschring 13-15 |
![]() |
63329 Egelsbach |
![]() |
Tel.: +49 (0) 61 03 / 402 - 0 |
![]() |
Fax: +49 (0) 61 03 / 402 - 139 |
![]() |
E-Mail: info@smc.de |
![]() |
www.smc.de |
Mehr Informationen zu Diebold:
![]() |
Diebold Goldring Werkzeuge GmbH & Co. |
![]() |
An der Sägmühle 4 |
![]() |
72417 Jungingen |
![]() |
Telefon 07477 871-0 |
![]() |
Fax 07477 871-30 |
![]() |
E-Mail: kontakt@hsk.com |
![]() |
www.hsk.com |
War dieser Artikel für Sie hilfreich?
![]() |
![]() |
![]() |
![]() |
![]() |
Bitte bewerten Sie diese Seite durch Klick auf die Symbole.
Zugriffe heute: 2 - gesamt: 3848.