Auf schnellstem Weg durch die Produktion
Intelligentes Transportsystem von Knoll
Als „Multilinie“ bezeichnet STIEBEL ELTRON seine neue, hochflexible Produktionsanlage für Wärmepumpen. Ihre Besonderheit: Starre Förderstrecken mit Handarbeitsplätzen sind mit einzelnen Arbeits- und Prüfstationen via FTS verbunden. Eine Kopfsteuerung sorgt dafür, dass die verschiedenen Wärmepumpenmodelle ihren individuellen Weg zu den benötigten Montagestationen finden. KNOLL Maschinenbau lieferte die Fördertechnik und kümmerte sich um die intelligente Verkettung von Sensoren und Software.
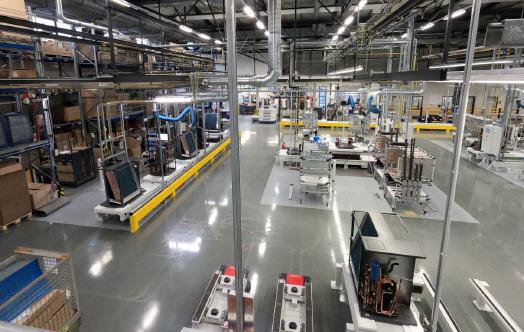
Wärmepumpen liegen im Trend. Die Absatzstatistiken der Verbände BDH (Bundesverband der Deutschen Heizungsindustrie) und BWP (Bundesverband Wärmepumpe) melden Jahr für Jahr Rekordzahlen. So sind 2021 allein in Deutschland rund 154.000 Heizungswärmepumpen neu installiert worden. Dazu kommen noch 23.500 Warmwasser-Wärmepumpen.
Einer der führenden Anbieter von Wärmepumpen für Heizung, Kühlung und Warmwasserbereitung ist STIEBEL ELTRON. Seit mehr als vierzig Jahren beschäftigt sich das Unternehmen am Stammsitz Holzminden mit deren Entwicklung und Produktion. Das Produktprogramm umfasst verschiedene Modelle – innen- und außenaufgestellte Wärmepumpen, Lösungen, nach dem Luft-Wasser-, Sole-Wasser- oder Wasser-Wasser-Prinzip, in verschiedenen Leistungsklassen und viele mehr.
Um der steigenden Nachfrage langfristig zu begegnen, beschloss das Unternehmen, die Wärmepumpen-Produktion weiter zu optimieren. Eine Aufgabe für die Abteilung „Rationalisierung und Betriebsmittel“. Leiter Jens Knaup beschreibt: „Unser Aufgabengebiet ist sehr vielfältig. Wir unterstützen bei der Auswahl, Beschaffung und Implementierung von unterschiedlichem Equipment. Das reicht von einer einzelnen Maschine bis hin zu umfangreichen Projekten, wie zum Beispiel einer optimierten Produktionsanlage für unsere Wärmepumpen.“
Knaup und sein Team arbeiten dabei stets in enger Abstimmung mit der entsprechenden Abteilung, sozusagen den „Inhouse-Kunden“. In der Regel werden verschiedene Konzepte ausgearbeitet und bewertet. Bevor es in die Detailplanung geht, erfolgt die Abstimmung mit den Auftraggebern. Dann werden gegebenenfalls externe Partner eingebunden, mit denen die Pläne umgesetzt werden können.
Neues Konzept: die Multilinie für Wärmepumpen
So wurde auch bei der Optimierung der Wärmepumpen-Produktion am Standort Holzminden verfahren. Die Leitung des Projektes übernahm Roman Flegel, einer der Mitarbeiter von Jens Knaup: „Wir starteten Anfang 2019 mit der Analyse der Ausgangssituation.“ Damals gab es verschiedene modellbezogene Fertigungslinien, in denen Wärmepumpen händisch auf Montagewagen von Arbeitsplatz zu Arbeitsplatz geschoben wurden – ein wenig flexibles und im Störungsfall auch zeitintensives Konzept.
„Die Aufgabenstellung war von vornherein, eine hochflexible Fertigungslösung zu implementieren“, berichtet der Maschinenbau- und Wirtschaftsingenieur, „in der wir trotz der hohen Diversifikation alle Wärmepumpentypen über eine Fertigungslinie produzieren können. So kann gewährleistet werden, auch zukünftig effizient und wirtschaftlich zu produzieren.“
Roman Flegel und seine Kollegen arbeiteten ein Konzept aus. Da die Montageabfolge der einzelnen Modelle unterschiedlich ist, war eine durchgängig starre Montagestrecke von Anfang an ausgeschlossen. „Wir brauchen hohe Flexibilität“, erklärt Flegel. „Die erreichen wir durch die Kombination von zwei kurzen Förderstrecken, die jeweils zwei Montagearbeitsplätze enthalten, mit separaten Lötarbeits- und Prüfstationen.“ Den individuellen Transport zwischen diesen Einheiten übernehmen Fahrerlose Transportsysteme (FTS). Für die Organisation der Abläufe ist eine im ERP verankerte Auftrags- und Kopfsteuerung zuständig, die alle Wärmepumpentypen und Arbeitsplätze einbezieht. „Kürzere Reaktionszeiten und die Möglichkeit, sogar neue Produkttypen oder Nullserien über die Multilinie zu fahren, sind die Vorteile“, sagt Flegel.
Jens Knaup weist auf die Hauptanforderung hin, die das innovative Anlagenkonzept zu erfüllen hatte: „Wir müssen unsere Produktinformationen mit intelligenten Fördersystemen und autonomen Transportfahrzeugen verknüpfen sowie Schnittstellen untereinander und zu unserem SAP ME-System schaffen. Das ist uns gemeinsam mit unseren Partnern hervorragend gelungen – ein echtes Vorzeigeprojekt in Sachen Digitalisierung und Industrie 4.0.“
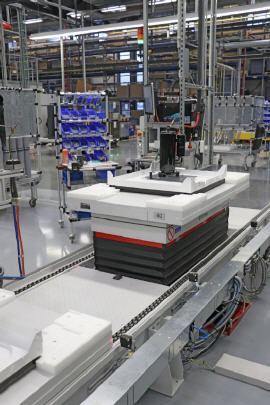
Erfolgreiche Partnersuche
Nach der Ausarbeitung des Konzepts war das Lastenheft bereits sehr konkret. Damit gingen die Anlagenplaner auf verschiedene FTS- und Fördertechnikanbieter zu und entschieden sich schließlich für die Firma KNOLL. Roman Flegel: „Mit der Fördertechnik von KNOLL Maschinenbau setzen wir ein System ein, das ein standardisiertes, modulares Design aufweist und damit der Herausforderung unserer Multilinie gewachsen ist. Die Möglichkeit, das System bei KNOLL in der Fertigung live zu erleben, hat bei unserer Entscheidung natürlich geholfen.“
Bei der Wahl des FTS-Anbieters fiel die Entscheidung zugunsten DS Automotion. „Die KNOLL-Transport- und Montagesysteme müssen perfekt mit den FTS harmonieren,“ erklärt Flegel. „Dass DS schon bei anderen Projekten mit KNOLL erfolgreich kooperierte, war ein wichtiges Kriterium.“ Die SAP-Integration übernahm das Ingenieur-Team von IGZ in Falkenberg.
Ein zentrales Element der Multilinie ist das Zusammenspiel von Transportbändern, Montagestationen, FTS und SAP ME mit der integrierten Anlagensteuerung. „Daher war es für uns wichtig, mit KNOLL einen Partner zu haben, der sich sowohl auf SPS-Seite zur Steuerung der Antriebe, Hubtische, Drehbewegungen etc. sehr gut auskennt, aber auch Schnittstellen-Know-how besitzt“, betont Roman Flegel. „KNOLL steuert außerdem die gesamte Sensorik bei, die an den Übergabestellen erforderlich ist.“
Multilinie entstand gewissermaßen im Bypass
Im Sommer 2020 erfolgte die Vergabe des Projektes an die genannten Zulieferer und Dienstleister. Im Laufe eines knappen Jahres gelang es STIEBEL ELTRON mit seinen Partnern, die Multilinie produktionsreif aufzubauen. Laut Jens Knaup ist das eine enorme Leistung, denn der Produktionsbetrieb musste wegen der hohen Auftragszahlen parallel weiterlaufen. „Teilweise wurde der Boden saniert, inklusive der farblichen Unterscheidung zwischen Fahrstrecken und Montagezonen“, so Knaup. „Das erforderte hohes organisatorisches Geschick und von allen beteiligten Partnern und Gewerken höchste Flexibilität.“
Das Ergebnis: Die Multilinie enthält an drei Stationen individell konfigurierte Transportsysteme von KNOLL, die über FTS miteinander verknüpft sind. Die FTS fahren in die Stationen ein und vollziehen dort einen Lastwechsel, um die Transportpalette abzugeben oder aufzunehmen. Neben diesen Aufnahme- und Abgabestationen wurden weitere Bearbeitungs- und Pufferstationen mit den KNOLL-Modulen realisiert. Die meisten Bearbeitungsstationen enthalten einen Hubtisch inklusive Drehplattform, mit dem die Mitarbeiter ihren Arbeitsplatz individuell und ergonomisch auf die eigenen Bedürfnisse anpassen können.
KNOLL entwickelte auch den universellen Werkstückträger, der so gestaltet ist, dass er alle Wärmepumpen-Modelle aufnehmen kann. 100 dieser Paletten sind in der Fertigung unterwegs. Der Werkstückträger mit den zu produzierenden Geräten wird mittels Förderband von der Bodenblech- zur Verdichtermontage und dann von den FTS zum Löten des Kältekreises gebracht. Dafür stehen vier verschiedene Arbeitsstationen zur Verfügung. Anschließend geht es zur sogenannten „Verdampferlinie“, einem Montageband mit zwei Stationen, in denen erst der Verdampfer eingebracht und anschließend gelötet wird. Je nach Pumpenmodell kann die Abfolge auch variieren. Am Ende steht aber immer die Druck- und Dichtigkeitsprüfung in der Prüfkammer an.
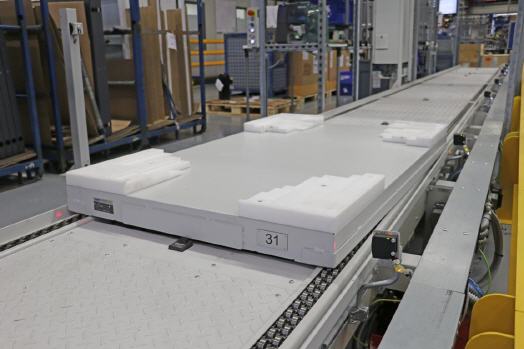
Erfolg auf der ganzen Linie
Seit der Inbetriebnahme im Sommer 2021 läuft die Anlage im Produktivbetrieb. Jens Knaup ist mit dem Ergebnis und der Partnerschaft mit KNOLL sehr zufrieden: „Das gilt für die Qualität der gelieferten Hardware in Form der Transportbänder und Handarbeitsplätze wie auch für die Bedienung der Hub- und Drehtische über Steuereinheiten an den Arbeitsplätzen: Sie ist einfach und dank Hardwaretaster störungsunanfällig realisiert.“
Projektmanager Roman Flegel lobt die von KNOLL erbrachte Dienstleistung im Bereich der Anlagensteuerung: „Die Zusammenarbeit war stets professionell und ergebnisorientiert. KNOLL war maßgeblich an der Programmierung der Schnittstellen zum fahrerlosen Transportsystem und SAP ME beteiligt. Die Systeme von KNOLL überwachen die Auf- und Abgabestationen und übermitteln die entsprechenden Daten an das SAP ME, das die Produkte über die Anlage leitet.“ Zudem hebt er die Flexibilität aller beteiligten Mitarbeiter hervor, die den Aufbau der Multilinie bei vollem Betrieb der Altanlage überhaupt erst möglich gemacht habe.
Auch die Produktionsverantwortlichen sind zufrieden. Durch die Implementierung zukunftsgerichteter Systeme und Prozesse sei es gelungen, die Produktivität deutlich zu steigern und eine enorme Transparenz zu erreichen. Jens Knaup: „Wir können jetzt zu jeder Zeit nachvollziehen, wo sich welches Produkt in welchem Zustand befindet. Dadurch erkennen wir, wo Engpässe entstehen, können entsprechend nachbessern und letztendlich die Kapazität erhöhen. Die Anlage ist so angelegt, dass wir – auf gleicher Fläche bei gleicher Anzahl Mitarbeiter – die Stückzahl verdoppeln können.“
Dieses Projekt sei zwar abgeschlossen, so Knaup, aber der Umbau der Wärmepumpen-Produktion sehe noch einen weiteren Schritt vor: „In der gleichen Halle findet auch die Endmontage der Wärmepumpen statt, in der sie final verdrahtet und isoliert werden. Am Ende erfolgen dann noch Endprüfung und Verpackung. Auch diese Schritte werden wir aller Voraussicht nach automatisieren.“
Mehr Informationen zu Knoll Maschinenbau:
![]() |
Knoll Maschinenbau |
![]() |
Schwarzachstraße 20 |
![]() |
88348 Bad Saulgau |
![]() |
Tel.: +49 (0) 75 81 / 20 08-0 |
![]() |
E-Mail: info.itworks@knoll-mb.de |
![]() |
www.knoll-mb.de |
War dieser Artikel für Sie hilfreich?
![]() |
![]() |
![]() |
![]() |
![]() |
Bitte bewerten Sie diese Seite durch Klick auf die Symbole.
Zugriffe heute: 2 - gesamt: 4583.