Für Robotik und CNC-Technologien
Eine einzige Programmierumgebung genügt
Seit fünf Jahrzehnten werden sowohl in der Robotik als auch im Bereich CNC enorme Fortschritte erzielt. Aber was bringt die Zusammenführung dieser beiden wichtigen Technologien? Ganz klare Wettbewerbsvorteile für Maschinenbauern und OEMs bei der Konstruktion von CNC-Bearbeitungszentren. Denn durch die Integration von Robotern in Werkzeugmaschinen können die Vorteile der Automatisierung voll ausgeschöpft werden und tragen zur Produktivitätssteigerung bei. Dank der Entwicklung einer einheitlichen Programmierumgebung für beide Technologien sind die Möglichkeiten nach oben offen.
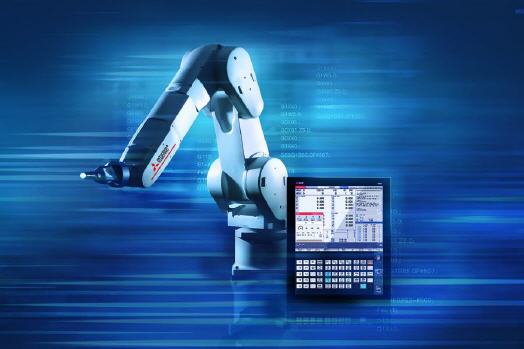
Die technologischen Entwicklungen der letzten 50 Jahre sind rasant. Produkte werden immer kleiner, schneller, leistungsfähiger, billiger und einfacher zu bedienen. Die Halbwertzeit von State-of-the-Art-Technologie beträgt nicht selten nur Monaten. Selbst im B2B Bereich, z.B. bei investitionsintensive Maschinen wird Rentabilität dank der gesteigerten Produktivität oft in Monaten statt früher in Jahren gemessen.
CNC-Bearbeitung und Robotik sind zwei gute Beispiele für diese rasante Entwicklung. CNC-Technologie (Computer Numerical Control) geht auf die Programmierung von Maschinen mit Lochkarten zurückgeht, und das war in den 1950er Jahren! Heute bieten CNC-Maschinen mehrachsiges, vollautomatisches, computergesteuertes Fräsen und Bearbeiten - eine relativ junge Innovation. Und damit ist ein wachsender Bedarf an Bedienern dieser Spezialausrüstung entstanden. Das Institute of Technical Trades US wagte schon 2016 die Behauptung, dass in den nächsten Jahren in vielen Branchen bis zu 40 % der Arbeitsplätze im Bereich der CNC-Technik liegen würden.
Sechs Jahrzehnte Roboter-Innovationen
Bei der Robotik sieht es ähnlich aus. Die ersten Industrieroboter wurden in den späten 1950er Jahren entwickelt. Der Unimate war 1961 der erste kommerziell genutzte Industrieroboter, der heiße Metallteile an einem Fließband von General Motors in New Jersey, USA, anhob und stapelte. Eine weitere bemerkenswerte Entwicklung fand 1969 statt, als die Standford University den ersten vollelektrischen 6-Achsen-Gelenkroboter vorstellte - eine Kombination aus Rotations-, Revoluten-, Prismen- und Kugelgelenken.
In den 1970er Jahren kamen die ersten Roboterarme, wie wir sie heute kennen, auf den Markt: PUMA-Arme (Programmable Universal Machine for Assembly), die nur mit Drehgelenken arbeiten, was die Beweglichkeit des Arms erhöht. Gleichzeitig wurde die elementare Datenverarbeitung zur Steuerung der Position des Arms eingeführt.
In den 1980er Jahren gab es einen neuen Ansatz in der Robotik: Die Universität Yamanashi in Japan leistete Pionierarbeit mit einer Robotertechnologie, die sie SCARA nannte - Selective Compliance Articulated Robot. Der Arm hatte nur vier Gelenke und konnte sich nur in X-, Y- und Z-Richtung bewegen - daher der Begriff "selektiv nachgiebig". Er hatte jedoch eine Reihe von Vorteilen gegenüber komplexeren 6-Achsen-Armen, darunter Geschwindigkeit, Platzbedarf und Preis. Mitsubishi Electric war eines der Unternehmen, die diese Technologie auf den Markt brachten. Kurz darauf folgte eine kompakte 6-Achsen-Version für mehr Flexibilität in komplexen Montageprozessen.
In den letzten 40 Jahren hat Mitsubishi Electric diese Entwicklungen mit der Entwicklung von etwa 14 verschiedenen Generationen von Roboterarmen fortgesetzt, die jeweils Verbesserungen gegenüber der vorherigen Generation aufweisen. Einige der größten Fortschritte liegen in der Verkürzung der Roboterzykluszeiten. Vergleicht man ein Robotermodell aus dem Jahr 1998 mit einem modernen Pendant, so ist die heutige Version sechsmal schneller. Im Gegensatz dazu sind die Geschwindigkeiten der schnellsten Straßenautos im gleichen Zeitraum nur um das 1,4-fache gestiegen, wie Auto Express berichtet.
Es ist nicht nur die Grundgeschwindigkeit des Arms, die sich verbessert hat; intelligente Steuerungen sorgen in den modernen Arme für starke Beschleunigungen und sanfte Bewegungen. Beides führt zu drastischen Verbesserungen der Zykluszeiten.
Auch die Zahl der Robotermodelle, die Mitsubishi Electric anbietet, ist gestiegen. Waren es ursprünglich weniger als 10, so gibt es heute über 160 verschiedene Varianten mit speziellen Modulen und Merkmalen, die auf die Anforderungen der verschiedenen Branchen zugeschnitten sind. Dazu gehören spezielle Beschichtungen für den Lebensmittel- und Getränkesektor oder spezielle Dichtungen für Reinraumanwendungen.
Im Bereich der Sicherheit gab es ebenfalls beeindruckende Entwicklungen. Ursprünglich arbeiteten Industrieroboter hinter festen Schutzvorrichtungen; heute sind Roboter mit Sicherheitsschnittstellen ausgestattet, die es ihnen ermöglichen, ohne feste Schutzvorrichtungen zu arbeiten und als Cobots wie dem MELFA ASSISTA sogar eng mit Menschen zusammenzuarbeiten, um ein neues Maß an Flexibilität in moderne Fertigungsprozesse zu bringen.
Technologien zur Robotersteuerung
So wie die Entwicklung der Computerisierung immer leistungsfähigere CNC-Maschinen hervorbrachte, so haben die Fortschritte bei den Steuerungssystemen die Einsatzmöglichkeiten von Robotern verändert. Frühe Roboterkonstruktionen basierten auf digitalen Signalen als Schnittstelle zwischen dem Roboter und dem übrigen Steuerungssystem der Maschine. Jetzt können der Roboter und die speicherprogrammierbare Steuerung (SPS) der Maschine in dieselbe Plattform integriert werden, was die Menge der zu übertragenden Daten und die Geschwindigkeit der Datenübertragung selbst erhöht.
Diese Datenverfügbarkeit hat neue Möglichkeiten zur Verbesserung der Produktivität und zur Erzielung einer maximalen Rendite aus den Anlagen eröffnet. Informationen über die Gesamtlaufzeit und die Leistung einzelner Komponenten innerhalb des Roboters können genutzt werden, um Informationen zur vorausschauenden Wartung bereitzustellen, wodurch unnötige Maschinenstillstände vermieden und ungeplante Ausfallzeiten reduziert werden können. Die Daten können auch in die Cloud übertragen werden, wo Roboter an verschiedenen Standorten entweder verwaltet oder verglichen werden können, um zu sehen, wie sie sich verhalten.
Auch die zugehörigen Technologien haben sich weiterentwickelt und Fortschritte gemacht. Es ist heute üblich, Sensoren am Ende der Roboterarme anzubringen, die die ausgeübte Kraft erkennen können, was die Qualität steigert. Wenn der Roboter beispielsweise ein Teil in ein anderes einführt, kann die Kraftrückmeldung an das Steuerungssystem ein wichtiger Bestandteil des Qualitätssicherungsprozesses sein.
Bildverarbeitungssensoren sind auch in Robotersystemen alltäglich geworden und ermöglichen die Führung des Roboters an die gewünschte Position. Wichtig ist, dass ihre Integration jetzt einfach und praktisch nahtlos ist.
Die vielleicht wichtigste Entwicklung hat sich bei der Software für die Programmierung von Robotern vollzogen. Diese Software-Tools vereinfachen den Prozess der Programmierung selbst komplexester Aufgaben. Denn sie ermöglichen eine vollständige Simulation der Systeme. So können Fehlkäufe der Hardware im Vorfeld sicher ausgeschlossen werden, was sowohl Konstrukteuren als auch ihren Kunden die Gewissheit gibt, dass ein System wie geplant funktioniert. Die Oberfläche wird hierbei wie bei der Drag & Drop Programmiersoftware RT-VisualBox immer bedienerfreundlicher.
Fortschritte in der Software sind das Herzstück der jüngsten Innovation: selbstgesteuerte Roboter, die mit Hilfe von Sensoren ihre Umgebung scannen und ihren Bewegungspfad planen, um Hindernissen auszuweichen - alles in Echtzeit. Dies bedeutet mehr Sicherheit, selbst wenn mehrere Roboter und Menschen im selben Raum arbeiten, denn es ermöglicht den Robotern, ohne Überwachung zu arbeiten.
Robotik und CNC vereint
Für die signifikante Steigerung des Gesamtdurchsatzes wurde in den letzten Jahren die Robotertechnik verstärkt in der Maschinenbeschickung für eine effiziente Be- und Entladung des Bearbeitungszentrums eingesetzt. Dies verkürzt die Zykluszeiten und steigert die Effizienz des gesamten Produktionsprozesses. Auch menschliche Arbeitskräfte können ihre Ressourcen so für komplexe Aufgaben nutzen. Während die Maschinenbediener den Prozess für Kleinserienaufträge konfigurieren, können größere Chargen eigenständig über Nacht laufen.
Bisher gab es allerdings eine große Herausforderung: Die Programmiersprache von modernen Robotern unterscheidet sich stark von der Programmiersprache G-Code, die für die Programmierung von CNC-Steuerungen eingesetzt wird. Ermöglicht die Programmierung von G-Codes zwar die relativ schnelle Einrichtung des Bearbeitungszentrums, ging der Geschwindigkeitsvorteil dann verloren, wenn der Maschinenbediener zusätzlich die skriptbasierte Programmiersprache der Robotik erlernen musste. Mitsubishi Electric hat diese beiden bisher getrennten Bereiche der Automatisierung mit der neuen Direct Robot Control für seine MELFA-Roboterfamilie zusammengeführt.
Bei dieser direkten Robotersteuerung werden Roboter und CNC nicht mehr separat programmiert, sondern der Roboter kann über G-Codes im CNC-Bearbeitungszentrum selbst programmiert werden. Der Roboter wird folglich als ein weiterer Teil des Bearbeitungsauftrags betrachtet. Er kann sogar mit dem Handrad der Maschine bewegt werden. Alle Alarme und Warnungen von Roboter und CNC werden darüber hinaus in derselben Protokolldatei aufgezeichnet.
Diese Innovation eröffnet eine ganze Reihe neuer Möglichkeiten. Unternehmen müssen in Zeiten des Fachkräftemangels einen Spezialisten, der beide Programmiersprachen beherrscht oder gar zwei spezialisierte Programmierer rekrutieren. Sie erleichtert den Erstausrüstern die Integration der Robotik in ihre CNC-Maschinenkonstruktionen und verschafft einen echten Wettbewerbsvorteil.
In den letzten 50 Jahren hat sich sowohl die Robotik als auch die CNC--Bearbeitung massiv weiterentwickelt. Die Gegenwart hat diese beiden Technologien wie nie zuvor zusammengebracht, und zweifellos wird diese Verbindung zukünftig noch enger. Ein Blick auf die Vorteile, die eng integrierte Roboter in anderen Bereichen gebracht haben, kann einige Hinweise darauf geben, was die Zukunft in der CNC-Welt bringen könnte.
Sicherlich kann mit einer verbesserten Anlagenverfügbarkeit gerechnet werden und vielleicht auch mit der Möglichkeit, einen höheren Automatisierungsgrad selbst bei der CNC-Bearbeitung mit hohen Stückzahlen und geringen Volumina zu erreichen. Da Technologien wie künstliche Intelligenz auch in die gängigen Automatisierungskomponenten Einzug halten, kann davon ausgegangen werden, dass maschinelles Lernen im robotergestützten Bearbeitungszentrum ebenfalls zu neuen Effizienzsteigerungen führen wird. Mitsubishi Electric ist hier mit seiner unternehmenseigenen KI-Technologie Maisart federführend.
Mehr Informationen zu Mitsubishi Electric Europe:
![]() |
Mitsubishi Electric Europe |
![]() |
Gothaer Straße 8 |
![]() |
40880 Ratingen |
![]() |
Tel.: 02102 486612-0 |
![]() |
Fax 02102 48670-90 |
![]() |
E-Mail: edm.sales@meg.mee.com |
![]() |
www.mitsubishi-edm.de |
War dieser Artikel für Sie hilfreich?
![]() |
![]() |
![]() |
![]() |
![]() |
Bitte bewerten Sie diese Seite durch Klick auf die Symbole.
Zugriffe heute: 3 - gesamt: 3873.