MPK Special Tools - tolerant bis zum letzten µ
Stanz- und Umformwerkzeuge in höchster Präzision
MPK Special Tools GmbH in Schwäbisch Gmünd ist auf die Bearbeitung von Hartmetall und Stahl spezialisiert. Rund 90 Prozent der hergestellten Stanz- und Umformwerkzeuge bestehen aus diesen Werkstoffen. Dabei durchläuft ein Bauteil meist sämtliche Fertigungsstufen bei dem 55-Mitarbeiter-Betrieb bis es zur fertigen Werkzeuglösung wird. Das umfasst Fräsen, Senk- und Drahterosion, Flachschleifen sowie Innen- und Außen-Rundschleifen. Seit über 20 Jahren werden für das Erodieren Sodick-Maschinen eingesetzt - allein fünf neue Maschinen seit Ende 2019. Erst im Januar wurde eine 25 Jahre alte Startlochbohrmaschine durch eine neue Sodick K1C für das Hochgeschwindigkeits-Startlochbohren ausgetauscht.
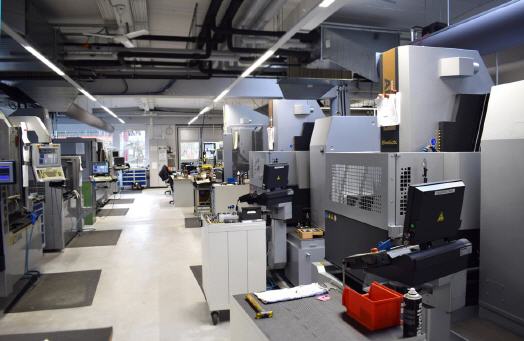
Der Präzisionsfertiger hat die letzten zweieinhalb Jahre genutzt und immens investiert, sowohl Maschinenpark als auch Räumlichkeiten sind komplett auf den aktuellen Stand gebracht worden. Der Maschinenpark lässt kaum Kundenwüsche offen, zumal sämtliche Fertigungstechnologien abgedeckt werden, alte Maschinen wurden entweder durch neue ersetzt oder einem umfassenden Retrofit unterzogen.
In den zurückliegenden drei Jahren haben rund 80 Kunden aus Elektronik-, Automobil-, Pharma- und Lebensmittelindustrie MPK Special Tools mit der Herstellung von Stanz- und Umformwerkzeugen beauftragt.
„Wir fertigen kundenspezifische Hartmetallwerkzeuge und Formbauteile auf Anfrage nach Zeichnung komplett, nur beim Beschichten nutzen wir die verlängerte Werkbank“, erklärt der Stellv. Betriebsleiter Christoph Steiner. „Diese Bauteile bekommt der Kunde in der Regel so nicht nach Norm von der Stange.“ Die Stückzahlen bewegen sich von Losgröße 1 bei Sonderwerkzeugen und reichen bis zu Kleinstserien mit 50 Bauteilen. Dabei sieht die MPK Special Tools ihre Stärken in der hohen Präzision, ein μ ist für den Tool-Spezialisten überhaupt kein Problem, und zwar über das Schleifen hinaus auch in den anderen Fertigungsbereichen. „Das ist natürlich immer ein wenig vom Bauteil abhängig, doch prinzipiell ist das μ bei uns richtig angesiedelt“, präzisiert Christoph Steiner. Um diese Genauigkeiten überhaupt garantieren zu können, ist die Fertigungshalle komplett klimatisiert, die Maschinen immer auf gleicher Betriebstemperatur.
Komplettservice über den ganzen Prozess
Damit das Ergebnis am Ende auch stimmt, wird präzise gemessen und dokumentiert. Bei MPK Special Tools geht kein Messauftrag nach außen. Die komplette Messtechnik mit eigenen Messarbeitsplätzen inklusive Endkontrolle befindet sich in der Fertigung. „Bei komplizierten Fertigungsprozessen ist es enorm wichtig bis zu den nächsten Fertigungsstufen permanent fertigungsbegleitend zu messen, um den Qualitätsstandard zu halten und zu überwachen“, weiß Christoph Steiner aus der Praxis. Und der Kunde erhält mit Auslieferung seines Präzisionsformwerkzeugs auf Wunsch ein Messprotokoll gleich mit.
Auch in punkto Umformtechnik verfügt MPK Special Tools über jahrelange Erfahrung. So werden beispielsweise Matrizen für Formwerkzeuge mit einer Stahlarmierung umgeben, damit diese entsprechend Kräfte aufnehmen können. Hierzu wird ein im Ofen erhitzter Stahlring ausgedehnt und über den Hartmetallkern geschrumpft. Durch das anschließende Abkühlen schrumpft der Stahlring auf den Hartmetallkern. „Obendrein bieten wir die Möglichkeit, dem Kunden je nach Wunsch eine Beschichtung mit anzubieten, um je nach Einsatzbereich zum Beispiel eine bessere Zieheigenschaft zu erreichen oder die Standzeit des Werkzeugs zu erhöhen“, hebt Christoph Steiner den Komplettservice hervor.
Eine Spezifikation ist zudem das Verzahnungsschleifen, wo unter anderem der Schwesterfirma ZECHA Hartmetall-Werkzeugfabrikation GmbH zugearbeitet wird. Bei der Sonderteilfertigung sowie mit Form- und Tiefziehwerkzeugen unterstützt MPK Special Tools die Schwesterfirma ebenfalls. „Wir haben auch schon in verlängerter Werkbank Kapazitäten übernommen, vor allem bei Sonderfällen im Erodieren, weil wir da wesentlich tiefer drin sind.“
Im Fertigungsbereich Erodieren unterscheidet sich die MPK Special Tools von klassischen Lohnerodierern. Alexander Winter, Leiter Draht-und Senkerosion, dazu: „Als Komplettbearbeiter bieten wir auch beim Erodieren das Gesamtpaket an Fertigungsknowhow von der Draht- und Senkerosion bis zum Startlochbohren.“ Für die Hartmetallbearbeitung kommen aufgrund ihrer hervorragenden elektrischen und thermischen Leitfähigkeit überwiegend Wolfram-Kupfer-Elektroden zum Einsatz. Die kleinsten damit erodierten Bauteile sind nicht größer als ein Fingernagel, die größten 200 auf 200 Millimeter, also klein und fein.
Neue Startlochbohr-EDM für noch mehr Präzision
Der Erodier-Bereich ist mit insgesamt 12 Sodick-Maschinen auf dem aktuellsten Stand: 5 Senk- und 5 Draht-Erodiermaschinen sowie 2 Startlochbohrmaschinen. Die erste eigene Sodick-Maschine war 1997 eine K1C-Startlochbohrmaschine. Die im Januar hinzugekommene Startlochbohr-EDM löste die 25 Jahre alte Maschine ab. „In 25 Jahren hatte die Sodick-Maschine kaum Reparaturen und ist immer noch funktionstüchtig, trotzdem war es an der Zeit sie nun auszusortieren“, sagt Erodierprofi Alexander Winter, der bereits seit 25 Jahren bei MPK Special Tools tätig ist.
Die neue K1C ist auf höchsten Durchsatz ausgelegt, mit der Option eines großen Tanks von 100 Litern speziell für die Hartmetallbearbeitung. Sie arbeitet nicht mit reinem Wasser, sondern mit einem Wasser-Öl-Gemisch, wodurch sich Mikrorisse merklich verringern und das bei höherer Verarbeitungsgeschwindigkeit. Die Weiterentwicklung im Generator macht sie noch genauer als das Vorgängermodell und kommt den hohen Präzisionsanforderungen von MPK Special Tools entgegen. „Sicher wären wir aufgrund unserer langjährigen Erfahrung mit Sodick-Maschinen in der Lage, so eine neue Maschine auch in Eigenregie zu installieren, alles ist logisch aufgebaut und zugänglich, trotzdem haben wir hier gern unseren langjährigen Maschinenpartner mit vor Ort“, sagt Alexander Winter.
Theoretisch ist so eine Startlochbohrmaschine innerhalb eines Tages installiert und inklusive Ersteinweisung einsatzfähig. Nach Anlieferung darf „die Neue“ sich aber erst einmal ein paar Tage „ausruhen“ und an die temperierte Umgebung anpassen. „Insbesondere bei den derzeitigen Außentemperaturen ist es vorteilhaft, seine Maschine zunächst ein paar Tage stehen zu lassen, damit sie sich an die Temperaturen anpasst“, empfiehlt auch Daniel Günzel seinen Kunden. „Die Maschine dankt es einem.“, so der Gebietsverkaufsleiter Baden-Württemberg von Sodick.
Erodieren auf höchstem Niveau
Ein Beispiel für die hohe Präzision ist die Fertigung von Matrizen, die nach einer Finish-Bearbeitung durch Polieren einen Ra-Wert von 0,025 an der Oberfläche aufweisen. Poliert wird dabei manuell, teils mit Filzen oder Polierhölzern. Gerade in diesem Bereich hat MPK Special Tools einige gelernte Uhrmacher beschäftigt. „Derartig spiegelglatte Polieroberflächen schaffen wir mit reinem Erodieren natürlich nicht“, weiß auch Daniel Günzel. Im Standard könne die Sodick-EDW im Ölbad mit acht Schnitten bereits eine Oberflächengüte von Ra 0,04 erreichen.
Ein anderer kundenspezifischer Auftrag war die Herstellung verschiedener Messeinheiten. Die Kundenvorgabe, bevor er mit dieser Messeinheit mit 2 Hundertstel Toleranz in Serie gehen konnte, lag bei 2 µ. „Wir haben die Messeinheit mit einer zehnmal höheren Genauigkeit hergestellt wie die später benötigte Wiederholgenauigkeit in der Fertigungslinie beim Kunden. So konnte er seine Bauteile von Anfang an sauber durchproduzieren“, erinnert sich Christoph Steiner.
Ebenfalls ein Alleinstellungsmerkmal von MPK Special Tools ist das Senkerodieren von Gewinden (M 1,6 bis M 30) in Hartmetall mit einer 6G-Toleranz beispielsweise für Spindelaufnahmen mit Hochpräzisionsgewinde. Bis in den Hundertstelbereich hinein wird hier von der Konturform der Funkenspalt reduziert - das ist extrem filigran. „Größere Gewinde schleifen wir auch, aber bei M 1,6 bleibt nur die hochgenaue Gewindeerosion auf Sodick-Maschinen. Wir benötigen dazu recht kleine Elektroden eben bis M1,6.“
Beim Senken werden zu 90 Prozent rotationssymmetrische Teile erodiert. Alle fünf Sodick-EDM sind deshalb mit Hochleistungsspindeln bestückt, die bis zu 2000 U/min erreichen. „Das ist schon eine Besonderheit“, weiß auch Daniel Günzel.
Mehrmaschinenbedienung intuitiv
Damit die Kleinserien möglichst mannlos durchlaufen, kommen Mehrfachvorrichtungen zum Einsatz. Diese haben sich die Erodierspezialisten bei MPK Special Tools selber ausgedacht und angefertigt. Die Maschine wird morgens gerüstet und läuft dann bis in den Nachmittag. In der Zwischenzeit können die Bediener eine andere Maschine rüsten bzw. programmieren. „Damit gehen unsere Umspannzeiten nahezu gegen Null, zumal der Werkzeugwechsel komplett automatisch erfolgt“, freut sich Alexander Winter. „Und für unsere Miniserien genügt die Stapelbearbeitung: Wir beladen den Tisch und dann wird der Stapel automatisch abgearbeitet.“ Auf diese Weise können die Maschinen mannlos auch übers Wochenende durchlaufen. Über das Netzwerk geben sie ihren Status weiter, und falls es zu einem Stillstand kommen sollte, beispielsweise wegen einer leeren Drahtspule, wird das erkannt und zurückgemeldet.
Von Vorteil für die Mehrmaschinenbedienung ist es, dass alle Sodick-EDM eine identische Steuerung haben. Wer eine Senkerodiermaschine bedienen kann, weiß auch, wo bei einer Drahterodiermaschine die Antastzyklen, die Wartungszyklen, die Koordinatenspeicher sind, das ist komplett identisch. Der Maschinenbediener muss so nicht von einem Maschinentyp auf den nächsten umdenken - auch das ist Prozesssicherheit. Selbst die neue Startlochbohrmaschine ist vom Start weg von jedem Werker bedienbar. Alexander Winter: „Da die Steuerungen über die Jahre immer aufeinander aufbauen und grundlegende Funktionen identisch sind, ist es ein leichtes, sofort mit der neuen Maschine loszulegen.“
Sämtliche Maschinen sind miteinander vernetzt und hängen an einem zentralen Server. Über das Netz werden die Programme zum Bearbeiten der Aufträge eingespielt. Da die Bediener ihre Programme selber erstellen und auch genau wissen, welche Spannvorrichtungen und Hilfsmittel sie brauchen, befindet sich ein zentraler Programmierplatz direkt in der Erodier-Abteilung. In einer Art Programmbibliothek sind alle Programme abgelegt. Sollte ein Bauteil nochmals gefertigt werden, zieht sich der Maschinenbediener das Programm auf die Maschine. Kommt ein ganz neuer Auftrag, setzt er sich an den Programmierplatz, schreibt das Programm und übergibt es anschließend an die Maschine. „Wir können dazu ähnliche Programme als Ausgangsbasis heranziehen und müssen so nicht immer bei Null anfangen, oft erhalten wir aber auch von Kunden schon bei der Angebotsanfrage ein 3D-Modell, aus dem wir direkt das Programm ableiten können“, erläutert Alexander Winter den Ablauf. Natürlich gebe es auch immer noch die Ausreißer, die nicht ganz mit der Zeit mitgegangen sind, von denen dann eine Handskizze kommt. Dann heißt es: selbst konstruieren / programmieren.
Wartung hochgeschraubt, Maschinenstillstand reduziert
Erodierprofi Alexander Winter kennt nach 25 Jahren bei MPK Special Tools so ziemlich alle Kniffe und sorgt dafür, dass keine Maschine längere Stillstandzeiten hat. Dabei spielt nicht nur der Kennerblick auf die Drahtspule eine Rolle, auch die Wartung und Pflege hat er mit seinem Team fest im Griff. Die fünf Maschinenbediener waren deshalb nicht nur zu Programmierschulungen bei Sodick in Düsseldorf, sondern speziell auch zur Fortbildung rund um die Maschinenwartung. „Seitdem achten wir darauf, dass alle Verschleiß- und Wartungsteile immer vorhanden und separat in einer Schublade für jeden verfügbar sind. So konnten Maschinenstillstände auf ein Minimum reduziert werden. Dort haben sie uns zudem noch gezeigt, wie der Umbau auf kleinere Drahtdurchmesser geht, da wir auch mit 0,1er Draht erodieren.“
Auch Stellv. Betriebsleiter Christoph Steiner ist von den Schulungen bei Sodick überzeugt: „So eine Schulung kostet zwar etwas, aber das wäre an der falschen Stelle gespart. Wenn eine Maschine einmal länger steht, verursacht das deutlich höhere Kosten.“ Und wenn aufgrund mangelnder Wartung ein Maschinenstillstand verursacht wird, entsteht ein Nadelöhr, wodurch der gesamte Fertigungsdurchlauf gestört ist.
Aus diesem Grund hatte der Fertigungsbetrieb übrigens 2020 ein Produktionsplanungssystem (PPS) eingeführt. Dort sind sämtliche Maschinen hinterlegt und alle Fertigungsaufträge werden darüber geplant. Der Maschinenbediener sieht jetzt anhand von Balkendiagrammen, welche Aufträge auf seiner Maschine anliegen. „Wenn wir dann eine Abteilung haben, welche die Wartung vernachlässigt, wäre das grob fahrlässig, dann können wir nämlich die Termine nicht einhalten“, gibt Christoph Steiner zu bedenken. Zudem könne jetzt auch einmal ein schneller Auftrag beispielsweise für eine Werkzeugreparatur über das PPS nebenbei mit durchgeschleust werden.
Grünen Fußabdruck hinterlassen
Auch mittelständische Fertigungsbetriebe wie MPK Special Tools beschäftigen sich heutzutage mit dem Thema Nachhaltigkeit. Künftig will MPK Special Tools die Abwärme der Maschinen rückführen und über einen Wärmeaustauscher zum Beheizen der Büroräume nutzen. „Immer mehr Kunden kommen auf uns zu und erwarten dies inzwischen von uns. Einige haben auch schon angekündigt, dass sie sich unsere Fertigungsmodernisierung anschauen möchten, um unseren „grünen Fußabdruck“ etwas nachverfolgen zu können“, so Christoph Steiner.
In den über zwei Jahrzehnten, in denen MPK Special Tools inzwischen Sodick-Maschinen einsetzt, ist ein enger partnerschaftlicher Kontakt entstanden. „Wie gut wir mit Sodick zusammenarbeiten, sieht man doch schon daran, dass wir inzwischen komplett mit den japanischen EDM-Maschinen ausgestattet sind über alle Erodier-Bearbeitungen“, so das Fazit von Christoph Steiner. „Für mich ist das auch der bessere Weg, wenn man sich für einen Maschinenpartner entscheidet und den Weg dann gemeinsam geht.“
Zudem müsse er so nicht unterschiedliches Maschinen-Knowhow vorhalten, unterschiedliche Programmiersysteme beherrschen, usw. - und wenn doch einmal ein Problem vorliegt, gibt es eine Hotline mit fachlich versiertem Personal bei Sodick. „Da sitzt nicht irgendein Callcenter am andern Ende, sondern ausgebildete Experten, die die Maschinen in- und auswendig kennen. Die meisten Problemfälle können wir unmittelbar am Telefon lösen und es muss erst gar kein Servicetechniker zu uns anreisen, wodurch sich die Stillstandzeiten ebenfalls reduzieren“, ist Alexander Winter überzeugt. Ein zusätzlicher Benefit: Der Hotline-Service von Sodick ist über den gesamten Lebenszyklus einer Maschine kostenfrei.
Dass die Sodick-EDM überaus robust sind, kann Alexander Winter nur bestätigen: „Ausfälle haben wir ohnehin nur aufgrund von Drahtende.“ Wie lange eine Drahtspule noch reicht, hat der erfahrene Erodierprofi im Blick. „Wenn ich abends noch einen Langläufer auf der Maschine einrichte, dann schaue ich kurz auf die Drahtspule und wechsle sie bei Bedarf noch aus.“ Bei den neueren Maschinen muss er sich aber aufgrund einer integrierten Drahtüberwachung auch darum nicht mehr sorgen: Diese zeigt exakt an, wieviel Meter Draht noch auf der Spule sind und wieviel Meter zum Erodieren des nächsten Auftrags benötigt werden.
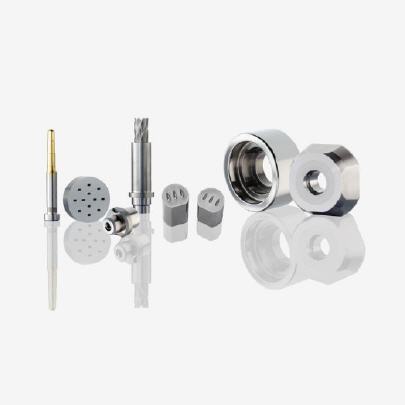
Mehr Informationen zur MPK Special Tools GmbH:
![]() |
MPK Special Tools GmbH |
![]() |
Hangendeinbacher Str. 4 |
![]() |
73527 Schwäbisch Gmünd |
![]() |
Tel.: +49 (0) 71 71 / 9 25 24-0 |
![]() |
Fax: +49 (0) 71 71 / 9 25 24-299 |
![]() |
E-Mail: info@mpk-specialtools.de |
![]() |
www.mpk-specialtools.de |
Mehr Informationen zu Sodick
![]() |
Sodick Deutschland GmbH |
![]() |
Mündelheimer Weg 57 |
![]() |
40472 Düsseldorf-Lichtenbroich |
![]() |
Tel.: +49 (0)211 422 608-0 |
![]() |
Fax: +49 (0)211 422 608-21 |
![]() |
E-Mail: info@sodick.de |
![]() |
www.sodick.de |
War dieser Artikel für Sie hilfreich?
![]() |
![]() |
![]() |
![]() |
![]() |
Bitte bewerten Sie diese Seite durch Klick auf die Symbole.
Zugriffe heute: 3 - gesamt: 4617.