Optimale Lagerbestände via Kanban
Fertigungssteuerung auf gute Art
Das jederzeit rechtzeitige Auffüllen zur Neige gehender Vorräte ist in der Industrie existenziell, soll es keine kostspielige Unterbrechung der Produktion geben. Nicht selten wird der dazu nötige Vorgang jedoch zu spät angestoßen, sodass hektische Improvisationen gestartet werden müssen. Die Konsequenz: Mehrfaches Umsortieren der Aufträge bis alles verfügbar ist, Eilbestellungen und verärgerte Kunden. Dabei gibt es eine zu jeder Betriebsgröße passende Methode zur Produktionsprozesssteuerung und Bestandsführung, die der Verknappung vorbeugt. Ihr Name: Kanban.
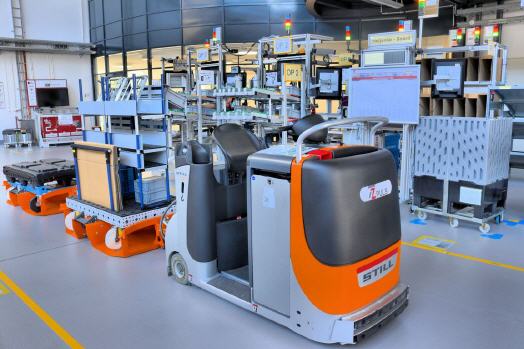
Ob Lebensmittel, Toilettenpapier oder Reinigungschemikalien – in einem gut geführten Haushalt sind regelmäßig benötigte Materialien stets in ausreichender Menge vorhanden. Man sieht sofort auf einen Blick, was zur Neige geht. Ausgehende Artikel werden auf einer Einkaufsliste notiert und beim nächsten Einkauf beschafft. In der Regel ist im Vorratsraum ein zweiter, gleichartiger Artikel, um beispielsweise Feiertage zu überbrücken, an denen die Geschäfte geschlossen sind. Diese Strategie – den Einkauf erst dann durchzuführen, wenn ein benötigtes Gut zur Neige geht – sorgt dafür, dass stets verbrauchsorientiert beschafft wird und somit eine kostenoptimale Bewirtschaftung des Haushalts erfolgt.
Dieser kleine Regelkreis für die Bewirtschaftung eines Haushalts beschreibt bereits das Grundprinzip eines Kanban-Systems, mit dem es möglich ist, kleine und große Unternehmen auf einfachste Weise mit benötigter Ware zu versorgen. Weit verbreitet ist der Irrglaube, dass dazu zwingend eine IT-Unterstützung nötig ist. Kanban kann jedoch ganz einfach mit einem Stück Papier, das einem Behälter beigelegt oder angesteckt wird, realisiert werden.
Diese ›Kanban-Karte‹ wird mit allen nötigen Informationen versehen, die für die Wiederauffüllung nötig sind. Dazu zählen: eine Materialnummer und Bezeichnung; die Materialquelle, also der Ort des Nachschubmaterials; die Materialsenke, das heißt, der Ort wohin das Material zu bringen ist; die Art des Behälters und die Menge der Teile pro Behälter. Wird das Kanban-System mit IT-Unterstützung betrieben, so wird der Karte zusätzlich ein Bar- oder ein QR-Code aufgedruckt oder ein RFID-Tag beigefügt.
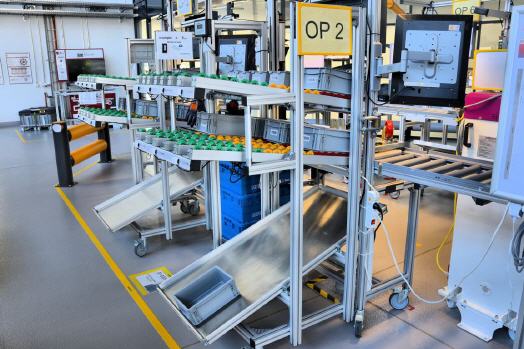
Kostenoptimale Produktion
Die Grundidee von Kanban ist es, möglichst niedrige Bestände bei hoher Termintreue und Flexibilität zu erreichen. Dazu muss man wissen, wie Kanban funktioniert, damit dies in der Praxis klappt: Die Produktion entnimmt sich die benötigten Teile aus dem Behälter im Regal. Sobald der Behälter leer ist, wird dieser auf einen festgelegten Leergutplatz gestellt. Der Logistiker kommt wie ein Bus zu definierten Zeiten an die Haltestellen und sammelt die leeren Behälter ein. Dabei nimmt er die Kanban-Karte vom Behälter ab und sammelt die Karten in einem Briefkasten.
Die gesammelten Karten entsprechen der Einkaufsliste, mit der der Logistiker jetzt im Supermarkt Nachschub besorgt. Dabei findet er mit den Daten auf der Kanban-Karte einen neuen, vollen Behälter, bringt die Karte wieder am Behälter an und transportiert diesen zurück in das Regal am Arbeitsplatz der Produktion. Je schneller dieser Kreislauf klappt, desto geringer können die Bestände sein. Das funktioniert im Übrigen nicht nur von der Produktion zum Supermarkt, sondern auch vom Supermarkt ins Lager und vom Lager zum Lieferanten.
Damit dieser Kreislauf auch wirklich funktioniert, sind einige Spielregeln einzuhalten:
- Es besteht grundsätzlich Hol-Pflicht. Der Verbraucher holt sich ein Material aus dem Puffer.
- Der Verbraucher darf nicht mehr Material anfordern, als er wirklich benötigt. Ein „Hamstern“ von Material ist ausgeschlossen, da dies den Bestand nur unnötig erhöht!
- Der Verbraucher darf Material nur dann anfordern, wann er es auch wirklich benötigt. Frühzeitiges Anfordern erhöht Bestand und das Chaos nimmt zu!
- Der interne oder externe Lieferant bringt und produziert nur das was gemäß Kanban-Karte verbraucht werde. Für mehr ist kein Platz oder Behälter da!
- Die bereitgestellten Teile sind einwandfrei.
- Es werden Standardbehälter eingesetzt. Die definierte Menge je Kanban und der klare Lieferort im Regal erfordern geregelte Standardbehälter. Sonst passt am Ende nichts mehr zusammen.
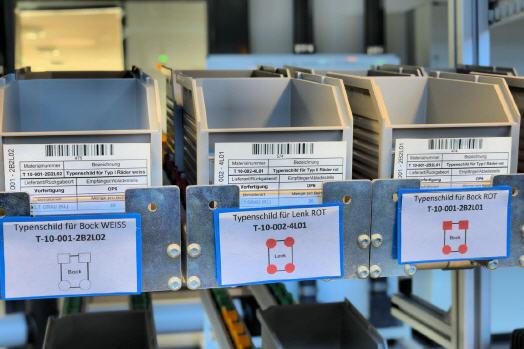
Es zeigt sich, dass Kanban ganz ohne EDV funktioniert. Die Steuerung des Systems klappt perfekt über die Leerbehälter unter Zuhilfenahme der Kanban-Karte. In diesem Zusammenhang ist interessant, dass der Name ›Kanban‹ aus dem Japanischen kommt und übersetzt so viel wie Karte, Tafel, Beleg, aber auch Behälter bedeutet. Entwickelt wurde Kanban im Jahre 1947 vom Japaner Taiichi Ohno, der damals beim Autoproduzenten Toyota beschäftigt war und dort das Produktionssystem entscheidend mitentwickelte.
Seine Idee zu Kanban kam ihm beim Betrachten der Vorgehensweise im Supermarkt. Hier bedienen sich Kunden selbst, während die Supermarktmitarbeiter damit beschäftigt sind, die sich leerenden Regale wieder zu befüllen. Die von ihm entwickelte Methode, eine Produktion als sich selbst regulierenden Arbeitskreis aufzubauen, hat viele Unternehmen inspiriert, sein System einzuführen. Lohn dieser Maßnahme sind massiv sinkende Lagerbestände, was mit stark abfallender Kapitalbindung einhergeht.
Natürlich kann Kanban auch mit moderner Technik verwoben werden. So ist es beispielsweise möglich, die Kanban-Karte in Papierform gegen ein elektronisches Display auszutauschen oder über Barcode beziehungsweise QR-Code die Verbräuche per ERP-System zu erfassen.
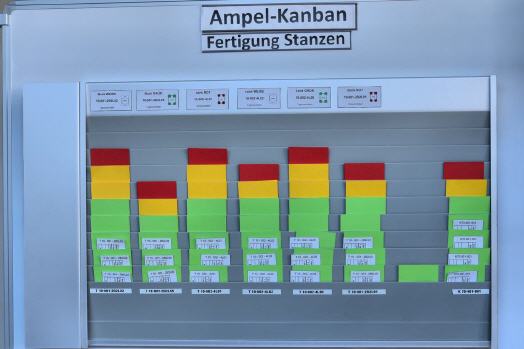
Offen für Bit und Byte
Auch mit RFID-Chips ausgerüstete Behälter warten mit Mehrwert auf. So können die Informationen der Kanban-Karte zusätzlich auf dem RFID-Chip hinterlegt werden. Wird der leere Behälter auf einen Stellplatz mit RFID-Lesegerät gestellt, kann so automatisch der Verbrauch an die Quelle beziehungsweise den Lieferanten übermittelt werden. Ganz ohne mühseligen und langsamen Kartentransport.
Ein Kanban-System auf RFID-Basis hat somit den Vorteil, dass die Durchlaufzeiten vom leeren Behälter bis zum Bereitstellen des neu befüllten Behälters ohne großen Aufwand ermittelt werden können. Dies birgt Potenzial für Optimierungen. Der größte Vorteil von Kanban ist jedoch zweifelsohne das Vermeiden von unnötig großen Lagerbeständen, was sich nicht zuletzt in der besseren Liquidität des Unternehmens darstellt.
Dies betrifft nicht nur die Montage, sondern auch die Fertigung von Einzelteilen für ein herzustellendes Produkt. Wird Kanban eingesetzt, so sorgt dieses System dafür, dass nur dann Teile produziert werden, wenn der Verbraucher die Teile auch wirklich benötigt. Die terminorientierte Auftragsbearbeitung wird demnach durch eine verbrauchsorientierte Auftragsbearbeitung ersetzt. Anders ausgedrückt kann gesagt werden, dass eine Push-Steuerung durch eine Pull-Steuerung ersetzt wird. Sich selbst steuernde Regelkreise sorgen für eine jederzeitige Versorgung der einzelnen Fertigungsbereiche, ohne dass eine zentrale Planungsinstanz nötig wäre.
Der wahre Treiber der Produktion ist letztlich der Kundenauftrag. Ausgehend vom allerletzten Schritt – oft einer Montage – wird im Kanban-System der Verbrauch der Teile durch „Ziehen“ geregelt. Alle vorgelagerten Stufen bis zum Rohmaterial liefern das nach, was vom vorgelagerten Prozess verbraucht wurde. Der klassische Materialdisponent wird so entlastet – das Kanbansystem regelt sich von allein. Wichtig ist jedoch je Teil die durchschnittlichen Verbräuche sowie den Wiederbeschaffungszeitraum zu ermitteln. Dieser ist für jedes Teil beziehungsweise jede Baugruppe individuell.
Insbesondere der Wiederbeschaffungszeitraum von extern zu beziehenden Komponenten und Materialien ist zu beachten, damit Engpässe vermieden werden. Der durchschnittliche Verbrauch und die Wiederbeschaffungszeit entscheiden über die Anzahl der Kanbans – und damit über die Bestandsmenge je Teil.
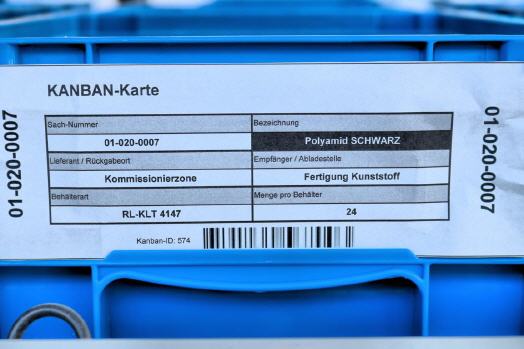
Vielseitig einsetzbar
Kanban ist ein sehr flexibles System. Damit ist es sogar problemlos möglich, Werkzeugausgabe-Automaten zu betreiben. Unter Berücksichtigung von Verbrauchsmenge pro Zeiteinheit und der Wiederbeschaffungszeit wird ermittelt, wie viele Fächer beispielsweise für eine bestimmte Wendeschneidplatte oder einen bestimmten Bohrer bereitgestellt werden müssen. Die Gesamtzahl der Fächer je Produkt entspricht zwei Behältern in der Fertigung. Ist die Hälfte der Fächer leer, so wird ein Bestellvorgang beim Betreiber des Werkzeugausgabeautomaten ausgelöst, der die leeren Fächer bei seiner Tour wieder befüllt.
Mittlerweile sind sogar Simulationssysteme am Markt, die in schematischer Form eine Produktion nachbilden können. Damit kann mühelos ermittelt werden, ob die geplante Kanban-Umgebung wie gedacht funktioniert. Wer sich dann immer noch nicht sicher ist, ob er den Sprung auf das Kanban-System wagen soll, der ist gut beraten, Kontakt mit den Experten der PuLL Beratung GmbH aufzunehmen.
Als Ausrüster des Technologiezentrums Produktions- und Logistiksysteme (TZ PULS) der Hochschule Landshut demonstriert die PuLL Beratung GmbH in der Musterfabrik am Standort Dingolfing unterschiedliche Kanban-Systeme und Realisierungsformen in der Praxis. Weiterhin kann man dort anhand einer realen Fertigungsumgebung in Erfahrung bringen, auf welche Weise die eigene Fertigung fit für die Zukunft gemacht werden kann. Und dieser Einstieg muss nicht ausgesprochen teuer sein, den Kanban arbeitet perfekt ohne IT-Einsatz.
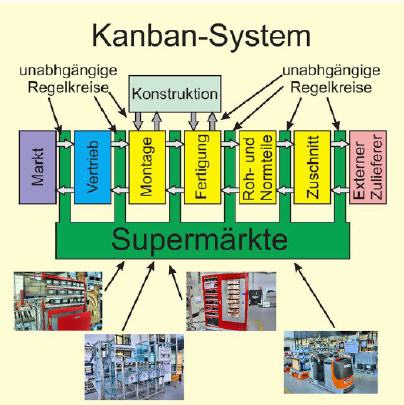
Download
Diesen Artikel finden Sie auch in Heft 1/2021 auf Seite 14. Zum besagten Heft führt ein Klick auf den nachfolgenden Button!
Mehr Informationen zur PuLL Beratung GmbH:
![]() |
PuLL Beratung GmbH |
![]() |
Schweriner Str. 1 |
![]() |
84036 Landshut |
![]() |
Tel.: 0871/95347394 |
![]() |
E-Mail: info@pull-beratung.de |
![]() |
www.pull-beratung.de |
War dieser Artikel für Sie hilfreich?
![]() |
![]() |
![]() |
![]() |
![]() |
Bitte bewerten Sie diese Seite durch Klick auf die Symbole.
Zugriffe heute: 1 - gesamt: 3605.