Schwingungsdämpfung via FVK
Ein altes Problem modern gelöst
Ob Werkzeug, Spannmittel oder Maschinenbauart – zahlreich sind die Stellschrauben, unerwünschte Schwingungen beim Zerspanen zu eliminieren. Einen außergewöhnlichen Weg, diesbezüglich zum Erfolg zu kommen, hat Benjamin Thorenz im Rahmen seiner Doktorarbeit gefunden: Ein Kern aus Faserverbundkunststoffen – bei dem die Fasern in einem ganz bestimmten Winkel aufgewickelt und kombiniert werden – der den geschaffenen Hohlraum eines Fräswerkzeugs ausfüllt.
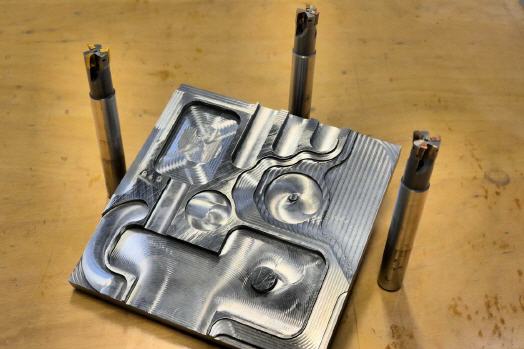
Auch alte Zerspanungs-Hasen staunen immer wieder über den Ideenreichtum vieler Forscher, Fräswerkzeuge noch leistungsstärker zu machen. Doch nutzen noch leistungsstärkere Beschichtungen, glattere Spanflächen oder ausgetüftelte Schneidenformen nur wenig, wenn der an- und abschwellende Schnittdruck – hervorgerufen durch die Spandickenänderung während des Fräsprozesses – das Fräswerkzeug in Schwingungen versetzt. Die Folgen sind ein erhöhter Verschleiß oder gar Bruch des Fräswerkzeugs sowie eine mangelhafte Oberflächengüte des zu bearbeitenden Werkstücks und letztendlich aufgrund geringerer Vorschübe eine unwirtschaftliche Zerspanung.
Nun gibt es bereits eine ganze Reihe von Lösungen, derartige Schwingungen zu unterdrücken. Diese reichen von Gummibändern, die vom Facharbeiter um das Werkzeug gewickelt werden, gehen über Federn im Werkzeugschaft und münden in Hartmetallstäben, die in Bohrungen der Werkzeugschäfte eingepresst werden. Zudem sind Hydraulik-Lösungen zu finden, bei denen es darum geht, per Stellschraube einen hohen Druck in der ölgefüllten Bohrung eines Werkzeugschafts zu erzeugen, was ebenfalls hilft, das Werkzeug gegen Schwingungen unempfindlicher zu machen.
Darüber hinaus gibt es sogenannte Hydrodehnspannfutter, bei denen mittels Hydraulikdruck der Werkzeugschaft mit maximaler Spannkraft geklemmt wird, während das Hydrauliköl zur Schwingungsdämpfung beiträgt.Stehen diese Lösungen nicht zur Verfügung, so kann man sich auch durch eine Variation der Schnittgeschwindigkeit, der Schnitttiefe oder des Vorschubs behelfen, was in der Regel jedoch mit höherer Fertigungs- beziehungsweise Durchlaufzeit einhergeht und somit die Stückkosten nach oben treibt. Doch hilft es schon, Fräswerkzeuge zu verwenden, die eine hybride Schneidengeometrie aufweisen.
Diese Werkzeuge wurden von Dr.-Ing. Hans-Henrik Westermann – einem ehemaligen Kollegen von Benjamin Thorenz – entwickelt und werden unter dem Produktnamen ›S-Cut‹ vom Werkzeughersteller Ceratizit vertrieben. Die Schneidengeometrie dieser Fräser sorgt für einen eher sinusförmigen Verlauf der Schnittkraft im Vergleich zu einem sägezahnförmigen bei Fräsern mit herkömmlichem Schneidendesign. Vielmehr bewirkt der Wechsel des Fräserdrallwinkels – der auf der ganzen Schneidenlänge erfolgt und sich zwischen 8 und 18 Grad bewegt – einen harmonischen Verlauf der Zerspankraft, was den Energiebedarf reduziert und Schwingungen deutlich vermindert.
Alle diese Ideen haben ihre Vorzüge und Grenzen. Sie versuchen auf unterschiedlichen Wegen Schwingungen beim Zerspanungsvorgang zu minimieren. Angesichts dieser Ideen-Fülle möchte man meinen, dass keine weiteren Lösungen existieren, Schwingungen beim Zerspanen zu eliminieren.
Doch weit gefehlt! Im Rahmen seiner Doktorarbeit hat Benjamin Thorenz den Beweis angetreten, dass hier noch nicht das letzte Wort gesprochen ist.
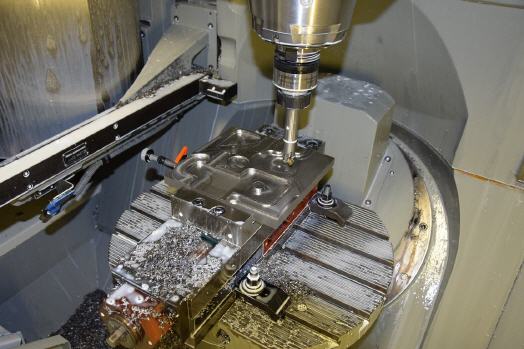
Zielführender Einfall
Seine Idee, Schwingungen zu dämpfen, beruht auf einem Stab aus Faserverbundkunststoffen (FVK), der in den Hohlraum eines Fräswerkzeuges eingeklebt wird. Was sich wenig spektakulär liest, ist eine echte Sensation in Sachen Dämpfung von Fräswerkzeugen. Und es ist erstaunlich, welche Stellschrauben gefunden werden mussten, um das Dämpfungs-Optimum zu erreichen. Dazu waren ausgetüftelte wissenschaftliche Arbeiten nötig, um das Potenzial dieser Lösung ans Tageslicht zu bringen.
So wurde beispielsweise per FEM-Berechnung der optimale Umschlingungswinkel berechnet, mit dem das Fasermaterial über einen Wickeldorn geführt wird. Der so hergestellte Stab wurde in den Hohlraum des Fräswerkzeug eingeklebt, wo er zu einer maximalen Reduzierung von Schwingungen während des Fräsvorgangs führt. Wie gut der FVK-Kern die Torsionskräfte beim Zerspanen aufnehmen kann, ist dabei unter anderem vom Umschlingungswinkel abhängig. Diese Tatsache, der Durchmesser des Kerns sowie die gewählten Materialien sind somit der entscheidende Kniff, um die Schwingungen von Zerspanungswerkzeugen zu reduzieren.
Die so produzierten Kerne wurden nach allen Regeln der Ingenieurskunst untersucht, um deren technischen Eigenschaften zu ermitteln. So wurden beispielsweise die Material-Kennwerte auf einer Universalprüfmaschine vom Typ 1475 des Herstellers ZwickRoell ermittelt, um ein Modell für Rechnersimulationen zu entwickeln. Dabei werden mit einem Kraftsensor die anliegende Kraft sowie mit einem Extensometer die Längenänderung von der Universalprüfmaschine erfasst. Durch die zusätzliche Applikation von Dehnungsmessstreifen konnten die Querkontraktionszahlen ermittelt werden. Natürlich wurde auch daran gedacht, Kerne von unterschiedlichem Durchmesser herzustellen, denn die Simulationsergebnisse zeigten, dass mitnichten die Dämpfungsqualitäten mit dem Kerndurchmesser wachsen.
Die Ergebnisse der Untersuchungen haben Benjamin Thorenz vollständig Recht gegeben, zudem eine faustdicke Überraschung ans Tageslicht gebracht: die kleinen Kerne zeigten die geringsten dynamischen Nachgiebigkeiten! Eingebracht in Fräswerkzeuge aus der Serie des Projektpartners Maier GmbH aus Oberschneiding führten diese Kerne aus dem Stand dazu, dass sich die Oberflächenqualität des Werkstücks im Vergleich zu Fräswerkzeugen ohne dämpfenden FVK-Kern um 30 Prozent verbesserte. Darüber hinaus konnte der Vorschub problemlos um rund 26 Prozent erhöht werden, sodass sich Fertigungsprozesse entsprechend zeitlich verkürzen, die Stückkosten demnach in dieser Größenordnung sinken. Doch ist dies noch nicht alles, denn auch die Standzeit verbesserte sich um 15 Prozent. Diese Verbesserungen zeigen, dass das Fräswerkzeug durch den FVK-Kern wirkungsvoll gedämpft wird.
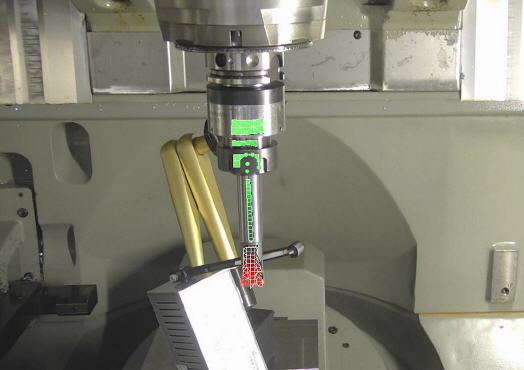
Ausgesprochen interessant ist, von Benjamin Thorenz zu erfahren, dass die Kleberwahl sowie die Größe und Ausführung des Klebespalts sich ganz entscheidend in den Ergebnissen bemerkbar machen. In den Versuchsreihen wurde mit Nuten unterschiedlichster Drallwinkel sowie mit Bohrungen unterschiedlicher Spaltmaße experimentiert. Es hat sich herausgestellt, dass auf Nuten verzichtet werden kann und eine Bohrung genügt, die 0,2 Millimeter größer ist als der Durchmesser des FVK-Kernes. Ferner ist bekannt, dass die maximale Klebfestigkeit bei einer weiteren Vergrößerung des Spalts wieder abnimmt.
Von größter Wichtigkeit ist in diesem Zusammenhang die Auswahl des Klebstoffs. Benjamin Thorenz setzt hier auf einen leistungsstarken Epoxid-Einkomponentenkleber mit ausgesprochen hoher Widerstandskraft gegen Stoß-, Scher-, Spalt- und Zugbelastung. Zudem besitzt dieses Produkt eine hohe Haltbarkeit, Chemikalienbeständigkeit und Hochtemperaturbeständigkeit, was gerade im Fall von Fräsern extrem wichtig ist, da diese während des Zerspanungsvorgangs sehr heiß werden. Darüber hinaus haftet dieser Klebstoff sogar auf öligem Stahl, was optimal im Umfeld einer Fräserproduktion ist.
Damit seine Fräsversuche nicht vom Zufall bestimmt werden, hat Benjamin Thorenz ein spezielles Testwerkstück entworfen mit dessen Hilfe sich genau ermitteln lässt, welche Auswirkungen unterschiedliche Parameteränderungen – wie etwa geänderter Kerndurchmesser, anderer Klebstoff, oder alternativer Wickelwinkel des Kerns – sich am Werkstück zeigen. Zudem wird mit einem Zerspankraftmessgerät, das sich zwischen Werkzeugmaschinenspindel und Fräserspannsystem befindet, sowie der Messung weiterer elektrischer Größen exakt festgehalten, welche Kombination aller Parameter zum geringsten Leistungsbedarf führt.
Die Fräser-Kern-Kombinationen wurden dabei in unterschiedlichsten Materialien – etwa C45 oder Inconel 713C – getestet und die jeweils resultierenden Werte ermittelt. Als Referenzwerkzeuge wurden Fräser mit einem Durchmesser von 20 Millimeter gewählt. Auf diese Weise wird aufgedeckt, wo sich Potenzial befindet, das lohnt, weitere Verfeinerungen hinsichtlich der Gestaltung des Kerns vorzunehmen.
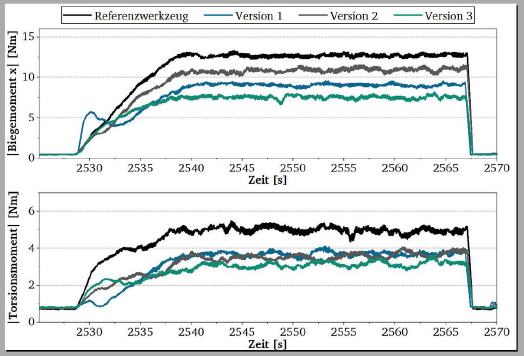
Das Ziel von Benjamin Thorenz war es, ein Fräswerkzeug-Dämpfungssystem zu entwickeln, das sich völlig unauffällig im Fräser integriert. Dieses Ziel brachte eine im Vorfeld der Forschung durchgeführte Marktbefragung zutage: Bei den Anwendern sind Dämpfungssysteme hochwillkommen, doch sollen sich die damit bestückten Fräser in der Handhabung nicht von herkömmlichen Fräswerkzeugen unterscheiden. Der Wunsch der befragten Personen war, auf schwingungsdämpfende Aufnahmen verzichten zu können.
Dieses Ziel ist mit dem in den Fräser eingeklebten FVK-Kern bestens erreicht, da der Fräser seine Schwingungsdämpfung mitbringt und keine zusätzlichen Anschaffungen nötig werden. Da der FVK-Kern sogar über eine Bohrung verfügt, geht auch nicht die Innenkühl-Funktion verloren. Somit wird diese Lösung all diejenigen Praktiker ansprechen, die ohne viel Aufwand zum optimalen Zerspanungsergebnis kommen möchten.
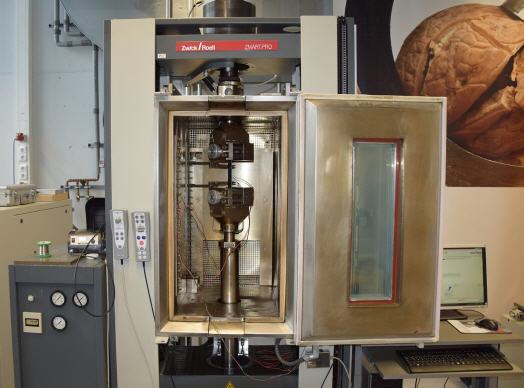
Download
Diesen Artikel finden Sie auch in Heft 6/2021 auf Seite 14. Zum besagten Heft führt ein Klick auf den nachfolgenden Button!
Mehr Informationen zur Universität Bayreuth:
![]() |
Universität Bayreuth |
![]() |
Lehrstuhl Umweltgerechte Produktionstechnik |
![]() |
Universitätsstraße 9 |
![]() |
95447 Bayreuth |
![]() |
Tel.: 0921 / 55-0 |
![]() |
Fax: 0921 / 55-5290 |
![]() |
E-Mail:info@uni-bayreuth.de |
![]() |
www.uni-bayreuth.de |
War dieser Artikel für Sie hilfreich?
![]() |
![]() |
![]() |
![]() |
![]() |
Bitte bewerten Sie diese Seite durch Klick auf die Symbole.
Zugriffe heute: 2 - gesamt: 1867.